Table of Contents
3+ Job Safety Observation Form Templates in PDF
Without a process in place that recognizes risk exposure before an accident or injury, companies will not achieve sustained excellent safety outcomes. Safety observation is a very productive practice that helps in the workplace to detect dangerous activities and unsafe conditions. When this process is carried out in a workplace or an organization, it is known as job safety observation. Observing and reporting on employees’ best practices also makes a difference in building a culture of protection across the company. A safety observation form is a tool that helps to determine the exact tasks that need to be performed for conducting the process.
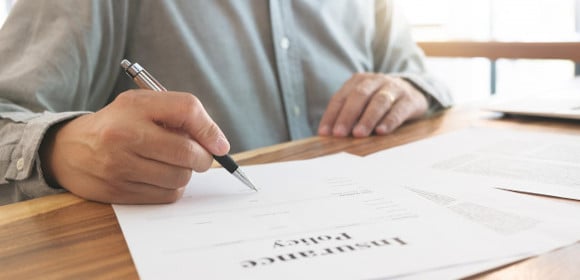
3+ Job Safety Observation Form Templates in PDF
1. Job Safety Observation Form
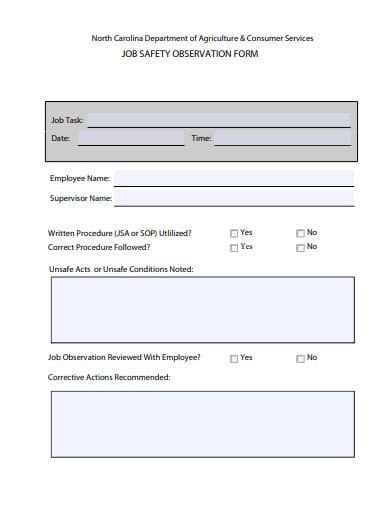
2. Sample Job Safety Observation Form
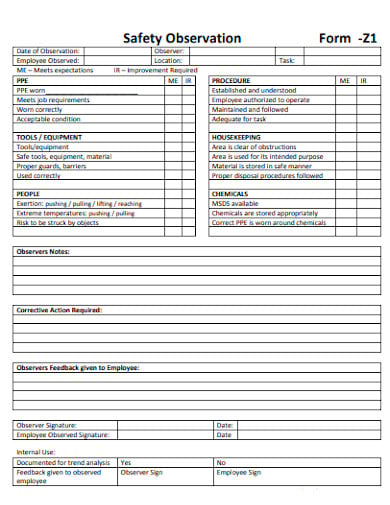
3. Company Job Safety Observation Form
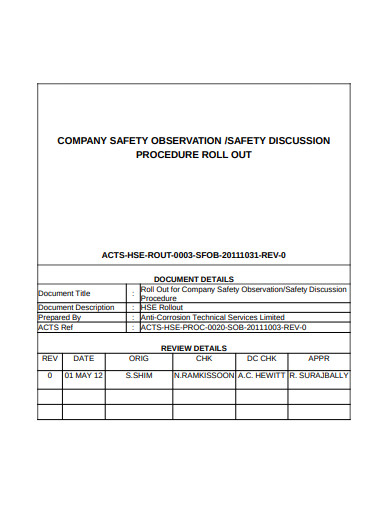
Types of Hazards or Risks in the Workplace
The first step, even before starting with observation process, is to know the types of hazards or risks that can exist in the workplace. Once you know what types of risks can arise or are already present, it will be much easier for the process to be carried out;
Type 1: Biological
A biological hazard is also known as biohazard. It is referred to as any biological substance that can pose a threat to the health of living beings, mainly humans. Such biohazards in the workplace include substances such as viruses, bacteria, insects, animals, etc. In other words, any such thing that can have adverse effects on health or be fatal. For example, mold, blood, vermin, dirt, etc.
Type 2: Physical
A physical hazard is an entity, element or situation that, without touch, may cause harm. Generally, they are listed under the occupational hazard category or under threats to the environment. In other words, they are anything that can cause bodily harm to the people surrounding it. For example, heights, noise, radiation, pressure, etc.
Type 3: Chemical
A chemical hazard is another type of occupational hazard resulting from workplace exposure to chemicals. Workplace exposure to chemicals can cause acute or long-term adverse effects on health. These safety risks can lead to both health and physical impacts, including irritation of the skin, irritation of the respiratory system, blindness, corrosion, etc.
Type 4: Ergonomic
Ergonomic hazards are physical conditions that may pose a risk of injury to the musculoskeletal system, such as lower back muscles or ligaments, hand/wrist tendons or nerves, or knee bones, resulting in a musculoskeletal disorder. Such risks include issues such as repetitive motion, manual handling, workplace configuration, awkward workstation height, and similar others.
Type 5: Safety
Safety risks are any condition or situation that creates or can pose unsafe working conditions. Exposed wires or a damaged carpet, for example, may result in a hazard of tripping. However, safety hazards are sometimes included in the physical hazards category.
Type 6: Psychosocial
A psychosocial hazard is the type of risk that can affect the psychological or/and the physical well-being of the employees. It can also affect their ability to take part in an environment of work among other people. Such type of hazards include sexual harassment, molestation, bullying, stress, violence, etc.
How to Identify the Risks in the Workplace?
The second step that needs to be followed before conducting a safety observation in any organization or institution is to know how to identify the risks in the workplace. The following highlights the steps on how you can identify the risks in your workplace;
- Collect information on existing risks likely to occur in the workplace.
- To identify new threats, perform daily site walkthroughs.
- To further examine the root causes and system defects, study injuries and near-miss records.
- Identify similar trends across all recorded incidents, illnesses, and dangers. Consider the risks involved in non-routine employment.
- Assess the level of risk of the hazard, importance, and frequency to determine which needs to be given priority.
5 Steps to Ensure a Smooth Safety Observation
Step 1: Announce
The first step in this process is to let the organization and its specific areas that you plan to observe, realize that you are there. The initial contact sets the tone for observation and the conversation arising from it.
Step 2: Watch
The second step involves the watch. You need to spend your assigned time watching the specific areas and the job roles after the employee is aware of that. The question that needs to be answered is what exactly is being looked for. The two general responses include if the task can be carried out safely and if there is any area that can cause worry. Lean behavior-based safety systems define what looks safe by identifying positively the few critical steps that workers may take to reduce the risk of accidents. The aim of this step should be to determine whether employees are able to perform the given tasks safely and recognize issues that may increase the likelihood of injury.
Step 3: Ask
Safety observation has several aspects. The most important one is to determine why a precaution had been taken, or had not been taken. This understanding is one of the most powerful strategies for influencing behavioral change and prioritizing efforts to improve safety. Sometimes people become complacent with a task. It is crucial that the person being examined understands the reason for the decisions that he makes, both those that reduce risk exposure and those that add risk exposure.
Step 4: Reinforce
A safety observation is a good opportunity to highlight clearly the positive things a person does for his or her own health. Reinforce basically means that emphasis should be put on improving the areas that are working safely already to ensure that it is not just by luck when it comes to avoidance of injury. If a person has undertaken a discretionary measure while doing his job, this is an excellent time to reiterate precisely what you have witnessed him doing, and urge him to proceed.
Step 5: Express Concern
The vocabulary used to provide feedback is important when defining danger during an evaluation. A preferred approach to expressing concern is to claim that someone is “at risk” and “unsafe.” When you select the last examples, your views are brought into the discussion that often compromise confidence and respect. If an observer is concerned about how a task is performed, this provides a better opportunity for a conversation that leads to an understanding of why risk is part of the task.