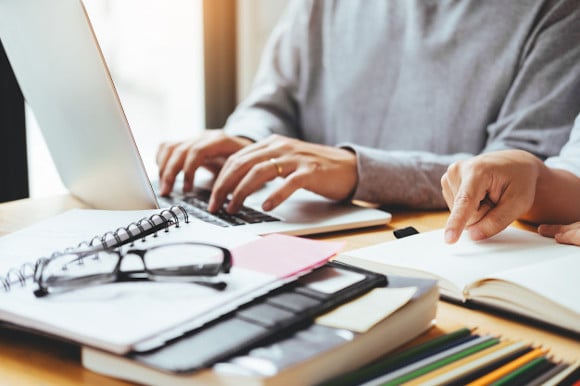
FREE 10+ Research Data Collection Form Templates in MS Word | PDF
In the research study, there are various important steps that are carried out every time and among these steps the…
Dec 30, 2020
Every single day, customers have a desire for different types of goods. All of these customers need to specify the kind of goods that they need to ensure that they get exactly what they asked for, which is they reason why there are times where order forms are utilized by these customers.
Order form templates allow these customers to specify details regarding what they would like to purchase. Even businesses can make use of this type of document in the event that they need to make internal orders for certain products and/or services. Those that know how to both create and utilize order forms are ensured to get whatever they need and/or want.
und.edu
mcallenisd.org
materials.ox.ac.uk
A material order form is basically what just about every business uses during the purchasing process to authorize the requisition of certain or all materials right before turning it into an purchase order. What this type of document does is to specifically order materials that will be used during the manufacturing process or materials that will be used for office operations. This kind of form should be handled by the production manager where he or she will be the one to fill it out. Then the manager will send the order to the material, storage, or purchasing department where he or she can then submit the form.
If you’re a production manager, then you’ll know just how important it is to know why these forms are being used. The first reason is that this form is a great way for you to be able to keep record of all the materials that are bought and used during the manufacturing process. Once your company has made the material order and has received what’s needed, they are then placed in the storage facility with the appropriate forms that need to be filled out. The point of the form is to who an audit trail that shows important information such as when the goods were purchased when they were delivered, and who issued the order. This document is also useful for knowing when goods were moved from storage to manufacturing.
The next reason as to why this form is so important is because it allocates production costs to the goods that need to be processed. While doing inventory management, production managers know that there will be some goods under process will not be finished within the current year. This means that there will always be a couple of goods that will still be in the production process. So to help you with your cost analysis, these forms will be able to allocate all of the values to every single material that was ordered.
There are five steps that you’ll have to do in order for you to gain the materials your business needs to conduct different operations. These steps are as follows:
This is basically the part where you make a formal request with the help of a material requisition form that you may fill out and send to your company’s purchasing department. The point of making a material requisition is that it informs the purchasing department about the need for you to have different materials bought for business-related purposes and it’s used to fix the responsibility to the specific department where the material requisition came from. The form can also be used during future references in the event that one needs to know who made the request, the materials that were requested, and the the purpose of the requisition.
Once the purchasing department has received the material requisition, they will then have to find the best source to purchase all of the materials that are being requested. The way to select the best possible supplier is by inviting quotations and tenders from every possible sources that can supply the company with the materials that it needs.
A purchase order form is basically what you send after you have chosen the supplier that you know can provide you with what your company needs. If the supplier accepts, then the form has basically become a contract agreement with the supplier, which states that he or she will provide you with the materials that you need and you will compensate by paying the supplier what he or she is owed for the service. These are usually prepared in five copies, so you’ll have to make sure that you have a copy for yourself in the event that it’s needed for future purposes.
Once the supplier has carried out the service and has delivered the materials, the receiving department will then be the ones that will perform the act of unloading and receiving the materials, as well as verifying the quantity and the condition of each and every single of one of them. This is very important as suppliers may end up with giving you materials that you never ordered, forgetting a number of materials that was listed, or handing out materials that are already damaged. Be sure that those in the receiving department are well trained in handling this service as it is very crucial in ensuring that everything is in place.
When you receive the official invoice from the supplier, you must then send this document over to the purchasing department where all of its contents will be verified. Assuming that there are no errors during the verification process, the purchasing department will then make a request to the company’s accounting department to make the payment to the supplier. The payment will be made according to the terms that have been specified within the contract. If there are any errors within the invoice, then this must be sent back to the supplier to make the proper corrections.
While the material purchasing process may differ from one company to another, it will always start with one issuing a material requisition order and end with the receipts of the cost of all the materials that have been purchased.
gmpsop.com
dent.umich.edu
sams.hkbu.edu.hk
phx.corporate-ir.net
arkansased.ov
Coming up with a material management plan is going to be a complex process that’s going to include the procurement, transportation, and inventory management from the manufacturer all the way to the storefront. This task will always be one that’s labor-intensive. So here are a few tips that should be able to help make the management process go a lot smoother.
In the research study, there are various important steps that are carried out every time and among these steps the…
Signing up for a book club? Starting a new career? Trying to buy items online? When doing any of these,…
There is no guarantee that everything you do will always go down just fine. And in a world where anything…
Recruitment authorization forms are very important in a company. These can be issued for various purposes. These forms are used…
A particular application form that can be considered as an official document that a potential employer may need some candidates…
Do you need to request petty cash to purchase any equipment or stationery material for a project? You can send…
In any event and social gathering, registrations forms are always on the record. They are important in tracking down the…
The one certain thing about hiring teachers is that you never know how good their skills are unless you evaluate…
Securing the future of your child is only possible when you give him the right environment, proper lessons, life values,…