Free Operations Supply Chain Risk Assessment
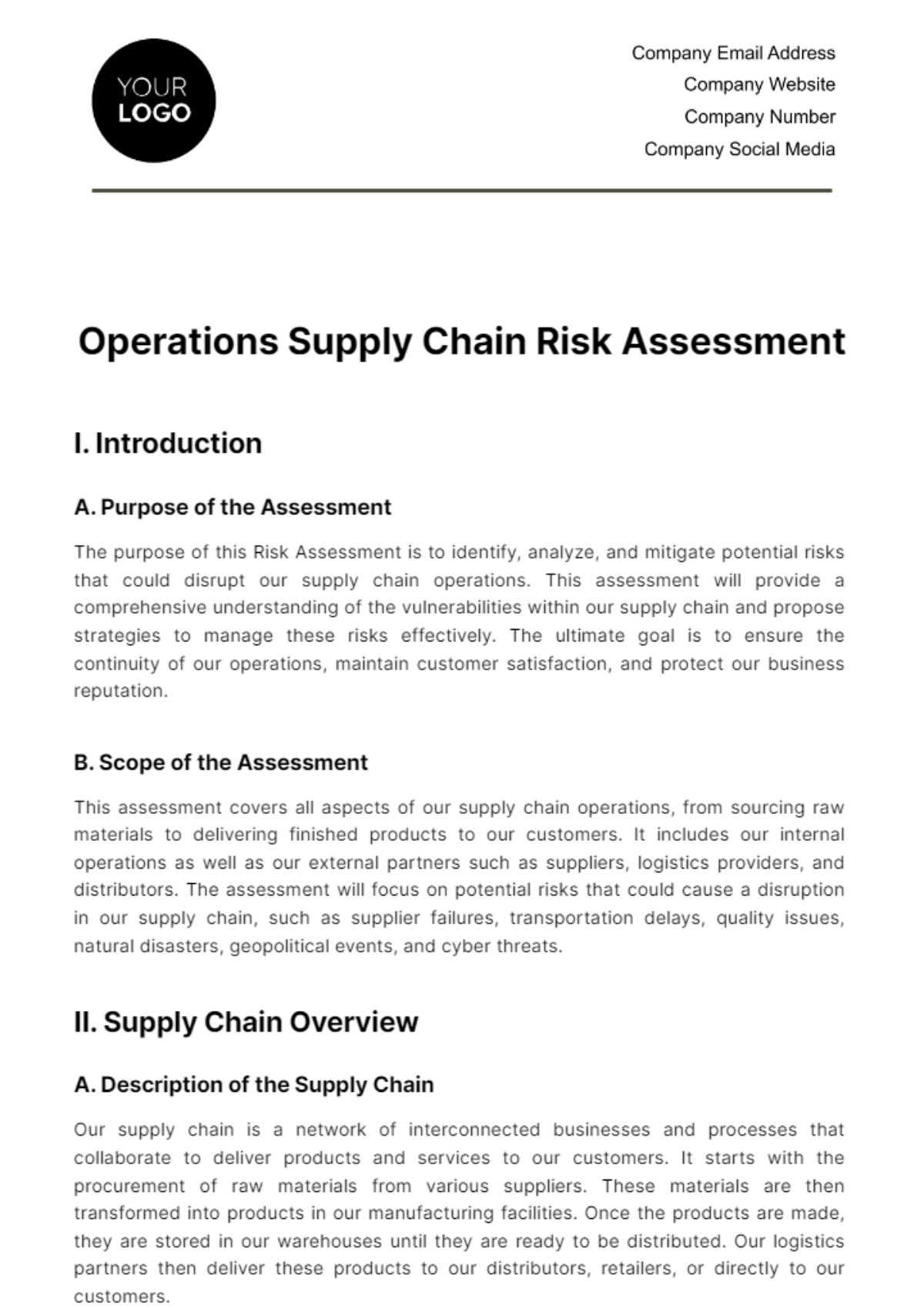
- 100% Customizable, free editor
- Access 1 Million+ Templates, photo’s & graphics
- Download or share as a template
- Click and replace photos, graphics, text, backgrounds
- Resize, crop, AI write & more
- Access advanced editor
Effectively mitigate supply chain risks with ease with the Operations Supply Chain Risk Assessment Template on Template.net! This editable template offers a customizable approach to assessing and managing risks in your supply chain. Use the AI Editor Tool for tailored edits, ensuring the assessment aligns with specific risk management strategies!
You may also like
Operations Supply Chain Risk Assessment
I. Introduction
A. Purpose of the Assessment
The purpose of this Risk Assessment is to identify, analyze, and mitigate potential risks that could disrupt our supply chain operations. This assessment will provide a comprehensive understanding of the vulnerabilities within our supply chain and propose strategies to manage these risks effectively. The ultimate goal is to ensure the continuity of our operations, maintain customer satisfaction, and protect our business reputation.
B. Scope of the Assessment
This assessment covers all aspects of our supply chain operations, from sourcing raw materials to delivering finished products to our customers. It includes our internal operations as well as our external partners such as suppliers, logistics providers, and distributors. The assessment will focus on potential risks that could cause a disruption in our supply chain, such as supplier failures, transportation delays, quality issues, natural disasters, geopolitical events, and cyber threats.
II. Supply Chain Overview
A. Description of the Supply Chain
Our supply chain is a network of interconnected businesses and processes that collaborate to deliver products and services to our customers. It starts with the procurement of raw materials from various suppliers. These materials are then transformed into products in our manufacturing facilities. Once the products are made, they are stored in our warehouses until they are ready to be distributed. Our logistics partners then deliver these products to our distributors, retailers, or directly to our customers.
Our supply chain also includes information flows, such as demand forecasts, order management, inventory levels, and delivery schedules. These information flows enable us to coordinate our supply chain activities and make informed decisions.
B. Key Stakeholders
Our key stakeholders include our suppliers, manufacturing facilities, warehouses, logistics providers, distributors, retailers, and customers. Each stakeholder plays a critical role in our supply chain and contributes to its overall performance. The key stakeholders are:
Suppliers: They provide the raw materials needed for our products. Their performance can affect our production schedules and product quality.
Manufacturing Facilities: They transform raw materials into finished products. Their efficiency and productivity can impact our production costs and lead times.
Warehouses: They store our products until they are ready for distribution. Their location and capacity can influence our delivery times and inventory costs.
Logistics Providers: They transport our products from one location to another. Their reliability and speed can affect our delivery performance and customer satisfaction.
Distributors and Retailers: They sell our products to the end customers. Their sales performance can impact our market share and revenue.
Customers: They are the end users of our products. Their satisfaction and loyalty can drive our future sales and growth.
III. Risk Identification and Analysis
A. Internal Risks
Internal risks are those that originate within our company and are usually under our control. Listed below are the internal risks:
Operational Risks: Operational risks are associated with our day-to-day operations. Production delays due to equipment failure can disrupt our supply chain and impact our ability to meet customer demand. Quality issues can lead to product recalls, damage our brand reputation, and result in loss of business. Therefore, it’s crucial that we have robust quality control and maintenance programs in place.
Strategic Risks: Strategic risks could affect our strategic objectives. A failure to innovate or adapt to changing market conditions can impact our competitive position and long-term profitability. It’s important that we continually monitor market trends and adjust our strategies accordingly.
Financial Risks: Financial risks are related to our financial management. Fluctuations in exchange rates or commodity prices can increase our costs and reduce our profit margins. To manage these risks, we need to have effective financial risk management strategies in place, such as hedging and diversification.
Human Resource Risks: Human resource risks are related to our people. A lack of skilled workers or high employee turnover can affect our productivity and operational efficiency. Therefore, we need to invest in employee training and development, and create a positive work environment to attract and retain talent.
B. External Risks
External risks are those that originate outside our organization and are usually beyond our control. These are the external risks:
Supplier Risks: Supplier risks are associated with the reliability and performance of our suppliers. A supplier failure or a disruption in the supply of raw materials can have a significant impact on our production schedules and costs. It’s important that we diversify our supplier base and establish strong relationships with our key suppliers to manage these risks.
Logistics Risks: Logistics risks are related to the transportation and delivery of our products. Delays in transportation, whether due to logistical issues or unforeseen events like natural disasters, can lead to increased lead times and missed delivery deadlines. Therefore, we need to work closely with our logistics providers and have contingency plans in place to manage these risks.
Market Risks: Market risks are related to changes in market conditions. Fluctuations in demand, changes in customer preferences, or the emergence of new competitors can affect our sales and profitability. To manage these risks, we need to continually monitor market trends and adjust our strategies accordingly.
Regulatory Risks: Regulatory risks are related to changes in laws and regulations. New environmental regulations, changes in trade policies, or changes in labor laws can affect our operations and increase our costs. Therefore, we need to stay informed about regulatory changes and ensure our compliance.
C. Likelihood of Risks
It is important to assess the likelihood of each identified risk as it helps in prioritizing risks and focusing on those that are most likely to occur. The following table provides an overview of these risks and their likelihood:
Risk | Likelihood |
---|---|
Production delays due to equipment failure | High |
Production delays due to equipment failure is a risk with a high likelihood. This means that, given the current conditions and controls, there is a high probability that our operations could experience production delays due to equipment failure. This could be due to various factors such as the age of our equipment, the frequency of maintenance, the quality of parts used, and the skill level of our operators.
Such delays could have significant impacts on our supply chain, including increased lead times, missed delivery deadlines, and increased costs. Therefore, it’s crucial that we have robust maintenance programs in place and that we train our operators properly to minimize the risk of equipment failure. We should also consider investing in newer, more reliable equipment if necessary.
For risks with a high likelihood, we need to focus on preventive measures to reduce the probability of the risk event occurring. For risks with a medium likelihood, we need to balance between preventive measures and contingency plans. For risks with a low likelihood, we may decide to accept the risk but have a contingency plan in place just in case the risk event does occur.
D. Impact of Risks
Assessing the impact of each identified risk helps in understanding the severity of the risk and aids in the decision-making process for risk mitigation strategies. Presented below are the risks and the potential impact:
Risk | Potential Impact |
---|---|
Production delays due to equipment failure | Increased lead times, missed delivery deadlines, increased costs |
Increased lead times can disrupt our supply chain and impact our ability to meet customer demand. Missed delivery deadlines can lead to customer dissatisfaction and potential loss of business. Increased costs can reduce our profit margins and affect our financial performance.
These impacts highlight the importance of maintaining our equipment properly and ensuring its reliable operation. We need to have robust maintenance programs in place and train our operators properly to minimize the risk of equipment failure. We should also consider investing in newer, more reliable equipment if necessary.
The assessment of the impact of risks is a critical step in our risk management process. It helps us to understand the severity of our risks and to develop appropriate risk management strategies. As we continue to monitor and review our risks, we should also update our assessment of risk impact to reflect any changes in our operations or our operating environment. This will ensure that our risk management process remains dynamic and responsive to our needs.
E. Risk Prioritization
Risk prioritization is a critical step in the risk management process. This helps us to focus our resources and efforts on the most significant risks. Here’s how we can prioritize the risks we’ve identified:
Risk | Likelihood | Impact | Priority |
---|---|---|---|
Production delays due to equipment failure | High | High | High |
Production delays due to equipment failure is a high-priority risk. This is because it has both a high likelihood and a high impact. This means that there is a high probability of this risk occurring, and if it does occur, it could have significant consequences for our supply chain. Therefore, we need to focus our risk management efforts on preventing this risk and reducing its potential impact.
This could involve implementing robust maintenance programs, training our operators properly, and investing in reliable equipment. By taking these measures, we can reduce the likelihood of equipment failure and minimize its impact on our production schedules, lead times, and costs.
It is important to note that not all risks are equal in terms of priority. This variation in priority highlights the importance of risk prioritization in our risk management process. It helps us to allocate our resources effectively and to focus our efforts on the most significant risks. By doing so, we can enhance the resilience of our supply chain and ensure the continuity of our operations.
IV. Risk Mitigation Strategies
Risk mitigation strategies are developed based on the results of the risk identification, analysis, and prioritization process. Here’s a detailed breakdown of the strategies:
A. Risk Prevention Measures
These are proactive steps taken to prevent a risk from occurring. They include:
Regular maintenance and inspection of equipment to prevent production delays.
Quality control measures to ensure product quality.
Regular training for employees to enhance their skills and productivity.
Financial risk management strategies such as hedging and diversification to manage financial risks.
B. Risk Reduction Measures
These are actions taken to reduce the impact of a risk. They include:
Diversifying suppliers to reduce the impact of a single supplier failure.
Having backup logistics providers to manage transportation risks.
Regular market analysis to stay ahead of market trends and customer preferences.
Ensuring compliance with laws and regulations to manage regulatory risks.
C. Contingency Planning
Contingency plans are developed to respond to a risk if it occurs. This includes:
Identifying the steps to be taken in response to a risk event.
Allocating the necessary resources to manage the risk.
Assigning responsibilities to individuals or teams.
Regular testing and updating of the contingency plans to ensure their effectiveness.
Each of these strategies plays a crucial role in managing supply chain risks. Risk prevention measures and risk reduction measures are proactive strategies that aim to prevent risks or reduce their impact. On the other hand, contingency planning is a reactive strategy that prepares the organization to respond effectively when a risk occurs.
V. Conclusion
In conclusion, this assessment is a critical aspect of managing and controlling risks within the company. It involves a systematic approach that starts with understanding the internal and external context of the organization, identifying potential risks, analyzing their likelihood and impact, prioritizing them based on these factors, and finally, developing effective risk mitigation strategies. This process not only helps in enhancing the resilience of the supply chain but also ensures the continuity of operations, thereby contributing to the overall success of the organization.
Furthermore, it’s important to note that risk management is a dynamic and ongoing process. As the business environment changes, the identified risks, their likelihood, impact, and the effectiveness of the mitigation strategies should be reviewed and updated regularly. This ensures that the risk management process remains responsive to the organization’s needs and continues to provide value. By taking a proactive approach to risk management, organizations can turn potential challenges into opportunities for growth and improvement.