AI
Marketing
Print
Document
Tools
Templates
Business
Categories
Marketing
Document
Free Workplace Incident Mitigation Strategy Plan
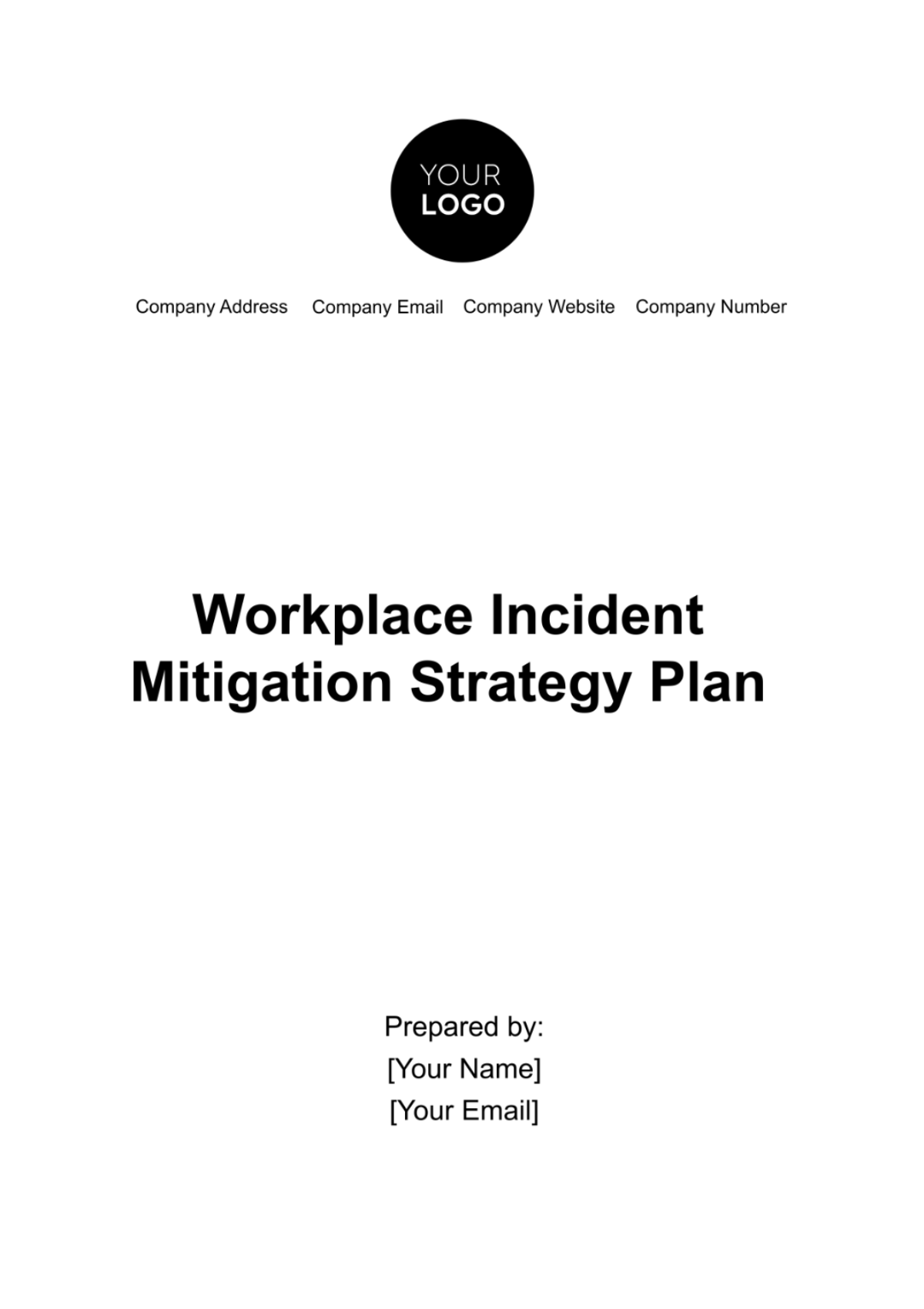
Free
No sign up needed
- 100% Customizable, free editor
- Access 1 Million+ Templates, photo’s & graphics
- Download or share as a template
- Click and replace photos, graphics, text, backgrounds
- Resize, crop, AI write & more
- Access advanced editor
You may also like
- Finance Plan
- Construction Plan
- Sales Plan
- Development Plan
- Career Plan
- Budget Plan
- HR Plan
- Education Plan
- Transition Plan
- Work Plan
- Training Plan
- Communication Plan
- Operation Plan
- Health And Safety Plan
- Strategy Plan
- Professional Development Plan
- Advertising Plan
- Risk Management Plan
- Restaurant Plan
- School Plan
- Nursing Home Patient Care Plan
- Nursing Care Plan
- Plan Event
- Startup Plan
- Social Media Plan
- Staffing Plan
- Annual Plan
- Content Plan
- Payment Plan
- Implementation Plan
- Hotel Plan
- Workout Plan
- Accounting Plan
- Campaign Plan
- Essay Plan
- 30 60 90 Day Plan
- Research Plan
- Recruitment Plan
- 90 Day Plan
- Quarterly Plan
- Emergency Plan
- 5 Year Plan
- Gym Plan
- Personal Plan
- IT and Software Plan
- Treatment Plan
- Real Estate Plan
- Law Firm Plan
- Healthcare Plan
- Improvement Plan
- Media Plan
- 5 Year Business Plan
- Learning Plan
- Marketing Campaign Plan
- Travel Agency Plan
- Cleaning Services Plan
- Interior Design Plan
- Performance Plan
- PR Plan
- Birth Plan
- Life Plan
- SEO Plan
- Disaster Recovery Plan
- Continuity Plan
- Launch Plan
- Legal Plan
- Behavior Plan
- Performance Improvement Plan
- Salon Plan
- Security Plan
- Security Management Plan
- Employee Development Plan
- Quality Plan
- Service Improvement Plan
- Growth Plan
- Incident Response Plan
- Basketball Plan
- Emergency Action Plan
- Product Launch Plan
- Spa Plan
- Employee Training Plan
- Data Analysis Plan
- Employee Action Plan
- Territory Plan
- Audit Plan
- Classroom Plan
- Activity Plan
- Parenting Plan
- Care Plan
- Project Execution Plan
- Exercise Plan
- Internship Plan
- Software Development Plan
- Continuous Improvement Plan
- Leave Plan
- 90 Day Sales Plan
- Advertising Agency Plan
- Employee Transition Plan
- Smart Action Plan
- Workplace Safety Plan
- Behavior Change Plan
- Contingency Plan
- Continuity of Operations Plan
- Health Plan
- Quality Control Plan
- Self Plan
- Sports Development Plan
- Change Management Plan
- Ecommerce Plan
- Personal Financial Plan
- Process Improvement Plan
- 30-60-90 Day Sales Plan
- Crisis Management Plan
- Engagement Plan
- Execution Plan
- Pandemic Plan
- Quality Assurance Plan
- Service Continuity Plan
- Agile Project Plan
- Fundraising Plan
- Job Transition Plan
- Asset Maintenance Plan
- Maintenance Plan
- Software Test Plan
- Staff Training and Development Plan
- 3 Year Plan
- Brand Activation Plan
- Release Plan
- Resource Plan
- Risk Mitigation Plan
- Teacher Plan
- 30 60 90 Day Plan for New Manager
- Food Safety Plan
- Food Truck Plan
- Hiring Plan
- Quality Management Plan
- Wellness Plan
- Behavior Intervention Plan
- Bonus Plan
- Investment Plan
- Maternity Leave Plan
- Pandemic Response Plan
- Succession Planning
- Coaching Plan
- Configuration Management Plan
- Remote Work Plan
- Self Care Plan
- Teaching Plan
- 100-Day Plan
- HACCP Plan
- Student Plan
- Sustainability Plan
- 30 60 90 Day Plan for Interview
- Access Plan
- Site Specific Safety Plan