Free Safety Performance Improvement Plan
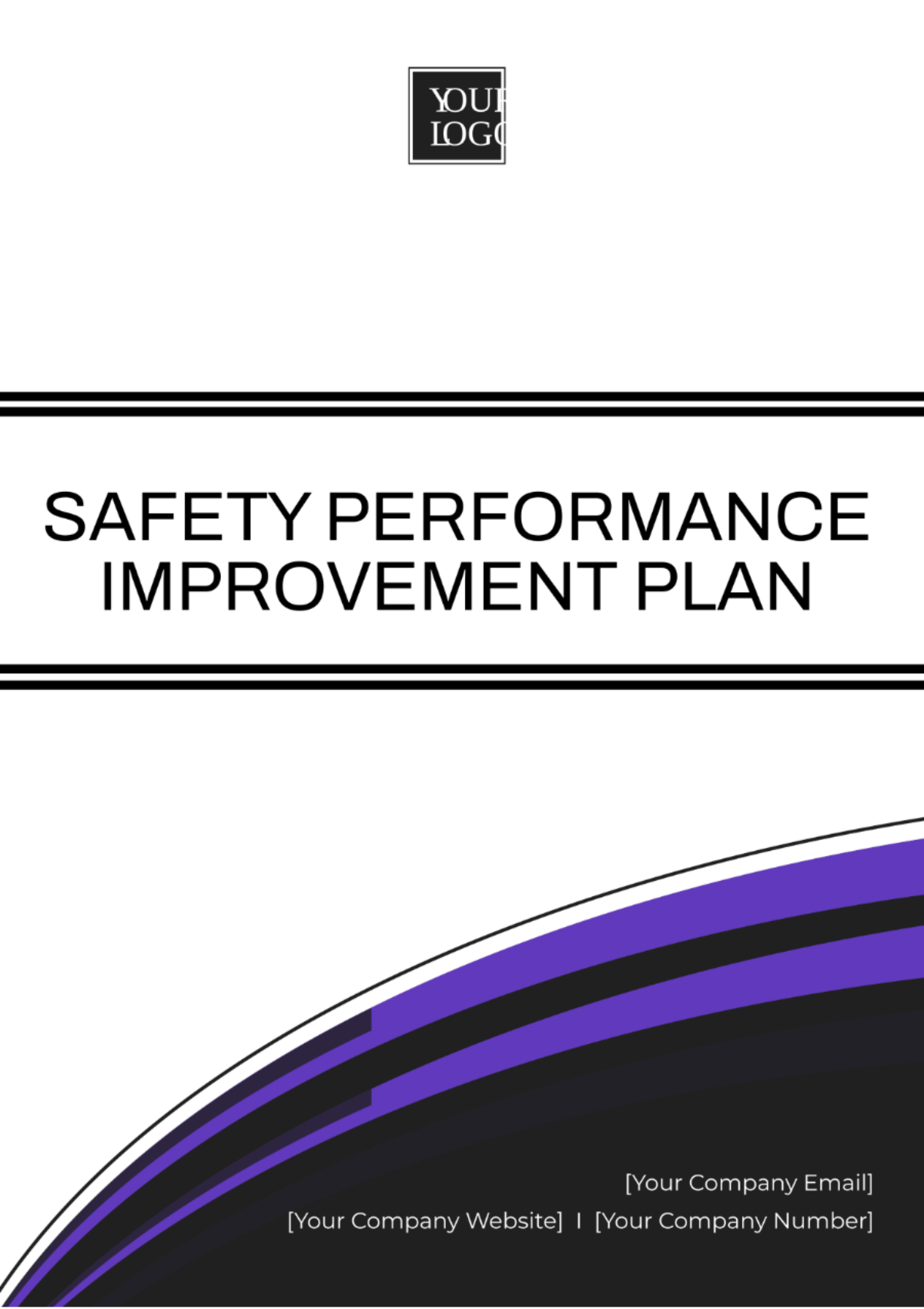
- 100% Customizable, free editor
- Access 1 Million+ Templates, photo’s & graphics
- Download or share as a template
- Click and replace photos, graphics, text, backgrounds
- Resize, crop, AI write & more
- Access advanced editor
Introducing Template.net's Safety Performance Improvement Plan Template—an editable and customizable solution designed to elevate safety standards effortlessly. Crafted to streamline safety initiatives, this template is user-friendly, editable in our AI tool, empowering you to tailor strategies with ease. Elevate safety culture seamlessly with this versatile resource.
You may also like
- Finance Plan
- Construction Plan
- Sales Plan
- Development Plan
- Career Plan
- Budget Plan
- HR Plan
- Education Plan
- Transition Plan
- Work Plan
- Training Plan
- Communication Plan
- Operation Plan
- Health And Safety Plan
- Strategy Plan
- Professional Development Plan
- Advertising Plan
- Risk Management Plan
- Restaurant Plan
- School Plan
- Nursing Home Patient Care Plan
- Nursing Care Plan
- Plan Event
- Startup Plan
- Social Media Plan
- Staffing Plan
- Annual Plan
- Content Plan
- Payment Plan
- Implementation Plan
- Hotel Plan
- Workout Plan
- Accounting Plan
- Campaign Plan
- Essay Plan
- 30 60 90 Day Plan
- Research Plan
- Recruitment Plan
- 90 Day Plan
- Quarterly Plan
- Emergency Plan
- 5 Year Plan
- Gym Plan
- Personal Plan
- IT and Software Plan
- Treatment Plan
- Real Estate Plan
- Law Firm Plan
- Healthcare Plan
- Improvement Plan
- Media Plan
- 5 Year Business Plan
- Learning Plan
- Marketing Campaign Plan
- Travel Agency Plan
- Cleaning Services Plan
- Interior Design Plan
- Performance Plan
- PR Plan
- Birth Plan
- Life Plan
- SEO Plan
- Disaster Recovery Plan
- Continuity Plan
- Launch Plan
- Legal Plan
- Behavior Plan
- Performance Improvement Plan
- Salon Plan
- Security Plan
- Security Management Plan
- Employee Development Plan
- Quality Plan
- Service Improvement Plan
- Growth Plan
- Incident Response Plan
- Basketball Plan
- Emergency Action Plan
- Product Launch Plan
- Spa Plan
- Employee Training Plan
- Data Analysis Plan
- Employee Action Plan
- Territory Plan
- Audit Plan
- Classroom Plan
- Activity Plan
- Parenting Plan
- Care Plan
- Project Execution Plan
- Exercise Plan
- Internship Plan
- Software Development Plan
- Continuous Improvement Plan
- Leave Plan
- 90 Day Sales Plan
- Advertising Agency Plan
- Employee Transition Plan
- Smart Action Plan
- Workplace Safety Plan
- Behavior Change Plan
- Contingency Plan
- Continuity of Operations Plan
- Health Plan
- Quality Control Plan
- Self Plan
- Sports Development Plan
- Change Management Plan
- Ecommerce Plan
- Personal Financial Plan
- Process Improvement Plan
- 30-60-90 Day Sales Plan
- Crisis Management Plan
- Engagement Plan
- Execution Plan
- Pandemic Plan
- Quality Assurance Plan
- Service Continuity Plan
- Agile Project Plan
- Fundraising Plan
- Job Transition Plan
- Asset Maintenance Plan
- Maintenance Plan
- Software Test Plan
- Staff Training and Development Plan
- 3 Year Plan
- Brand Activation Plan
- Release Plan
- Resource Plan
- Risk Mitigation Plan
- Teacher Plan
- 30 60 90 Day Plan for New Manager
- Food Safety Plan
- Food Truck Plan
- Hiring Plan
- Quality Management Plan
- Wellness Plan
- Behavior Intervention Plan
- Bonus Plan
- Investment Plan
- Maternity Leave Plan
- Pandemic Response Plan
- Succession Planning
- Coaching Plan
- Configuration Management Plan
- Remote Work Plan
- Self Care Plan
- Teaching Plan
- 100-Day Plan
- HACCP Plan
- Student Plan
- Sustainability Plan
- 30 60 90 Day Plan for Interview
- Access Plan
- Site Specific Safety Plan
Safety Performance Improvement Plan (SPIP)
Written by: [Your Name]
_____________________________________________________________________________________
I. Introduction
This section, provides an overview of the Safety Performance Improvement Plan (SPIP), its purpose, and its importance within the organization. Include a brief introduction to the organization's commitment to safety and the objectives of the SPIP.
II. Current State Analysis
In this section, conduct a comprehensive analysis of the current safety performance within the organization. Include data on incidents, near misses, hazards, and any relevant trends. Identify areas of improvement and prioritize them based on severity and potential impact.
Incident Data
Compile data on the number and types of safety incidents that have occurred within a specified period, including injuries, illnesses, property damage, and environmental incidents. Analyze trends over time to identify patterns and areas of concern.
Hazard Identification
Conduct a thorough assessment of workplace hazards, including physical, chemical, biological, ergonomic, and psychosocial hazards. Use techniques such as job hazard analysis (JHA) and safety inspections to identify and prioritize hazards based on their likelihood and potential consequences.
Safety Culture Assessment
Evaluate the organization's safety culture by assessing attitudes, beliefs, and behaviors related to safety among employees and leadership. Use surveys, interviews, and observations to gauge the level of safety awareness, commitment, and accountability within the organization.
III. Safety Goals and Objectives
Outline specific safety goals and objectives that the organization aims to achieve through the SPIP. Ensure that these goals are SMART (Specific, Measurable, Achievable, Relevant, Time-bound). Examples include reducing incident rates by a certain percentage or achieving certification in a safety management system.
Goal 1: Reduce Incident Rates
Objective 1.1: Decrease the total recordable incident rate (TRIR) by 20% within the next fiscal year.
Objective 1.2: Achieve zero lost-time incidents (LTIs) in high-risk areas by implementing targeted safety interventions and controls.
Goal 2: Enhance Safety Training and Awareness
Objective 2.1: Increase employee participation in safety training programs by 25% through improved scheduling and accessibility.
Objective 2.2: Ensure that 100% of employees receive annual refresher training on key safety topics, including hazard recognition and emergency procedures.
Goal 3: Strengthen Safety Leadership and Accountability
Objective 3.1: Implement a safety leadership training program for all managers and supervisors to enhance their knowledge and skills in safety management and communication.
Objective 3.2: Establish safety performance metrics and targets for departmental managers and supervisors, tied to performance evaluations and incentives.
IV. Action Plan
Develop a detailed action plan to address the identified safety issues and achieve the established goals. This plan should include:
A. Action Items
Conduct a comprehensive safety audit of all facilities and operations.
Implement a behavior-based safety program to promote safe practices among employees.
Enhance safety training programs to include hands-on exercises and simulations.
Install additional safety signage and barriers in high-risk areas.
Review and update safety procedures for handling hazardous materials.
B. Responsibilities
Safety Manager: Oversees the implementation of the action plan and coordinates with department heads.
Department Heads: Responsible for ensuring that action items within their departments are completed in a timely manner.
Safety Committee: Provides input and feedback on the action plan and assists in its implementation.
C. Timeline
Conduct safety audit
Implement behavior-based safety program
Enhance safety training programs
Install safety signage and barriers
Review and update safety procedures
D. Resources Required
Budget allocation for safety improvements.
Training materials and resources.
Personnel for conducting safety audits and implementing changes.
E. Monitoring and Evaluation
Regular safety inspections and audits to assess compliance with new procedures.
Feedback mechanisms for employees to report safety concerns and suggestions for improvement.
V. Training and Education
Outline a training and education program aimed at enhancing safety awareness and competency among employees. This may include:
A. Safety Training Modules
Hazard identification and risk assessment.
Emergency response procedures.
Proper use of personal protective equipment (PPE).
Safe handling of equipment and machinery.
B. Training Schedule
Monthly safety meetings to cover specific topics.
Quarterly hands-on training sessions.
Annual refresher courses for all employees.
C. Evaluation
Pre and post-training assessments to measure knowledge retention.
Feedback surveys to gauge the effectiveness of training programs.
Observations and performance evaluations to assess practical application of safety practices.
VI. Communication and Reporting
Establish clear communication channels for sharing safety-related information and reporting incidents or hazards. This may include:
Safety Meetings
Schedule regular safety meetings to discuss performance, share best practices, and address concerns.
Incident Reporting Procedure
Define a procedure for reporting incidents, near misses, and hazards.
Safety Alerts
Implement a system for issuing safety alerts or notifications to employees.
VII. Continuous Improvement
Highlight the importance of continuous improvement in safety performance. Encourage feedback from employees and stakeholders, and regularly review and update the SPIP to adapt to changing conditions and emerging risks.
Feedback Mechanisms:
Implement a suggestion box or online platform for employees to submit safety improvement ideas anonymously.
Performance Reviews:
Schedule regular performance reviews of safety metrics and key performance indicators (KPIs) to track progress towards safety goals.
Root Cause Analysis:
Conduct thorough investigations of incidents and near misses to identify underlying causes and implement corrective actions.
Training and Development:
Provide ongoing training and development opportunities for employees to enhance their safety knowledge and skills.
Leadership Engagement:
Foster a culture of safety leadership by encouraging managers and supervisors to lead by example and prioritize safety in their decision-making.
Continuous Review and Revision
Regularly review and update the SPIP to reflect changes in regulations, industry standards, and organizational priorities.
VIII. Appendices
Include any additional documents or resources that support the SPIP, such as incident report forms, training materials, or relevant policies and procedures.
Incident Report Form
A template for employees to report safety incidents, including fields for date, time, location, description of incident, and corrective actions taken.
Training Materials
Copies of training modules and presentations used in safety training sessions, covering topics such as hazard identification, emergency procedures, and PPE usage.
Safety Policies and Procedures
Copies of relevant policies and procedures related to safety management, including the organization's safety manual, emergency response plan, and risk assessment procedures.