Free Agriculture Safety SWOT Analysis
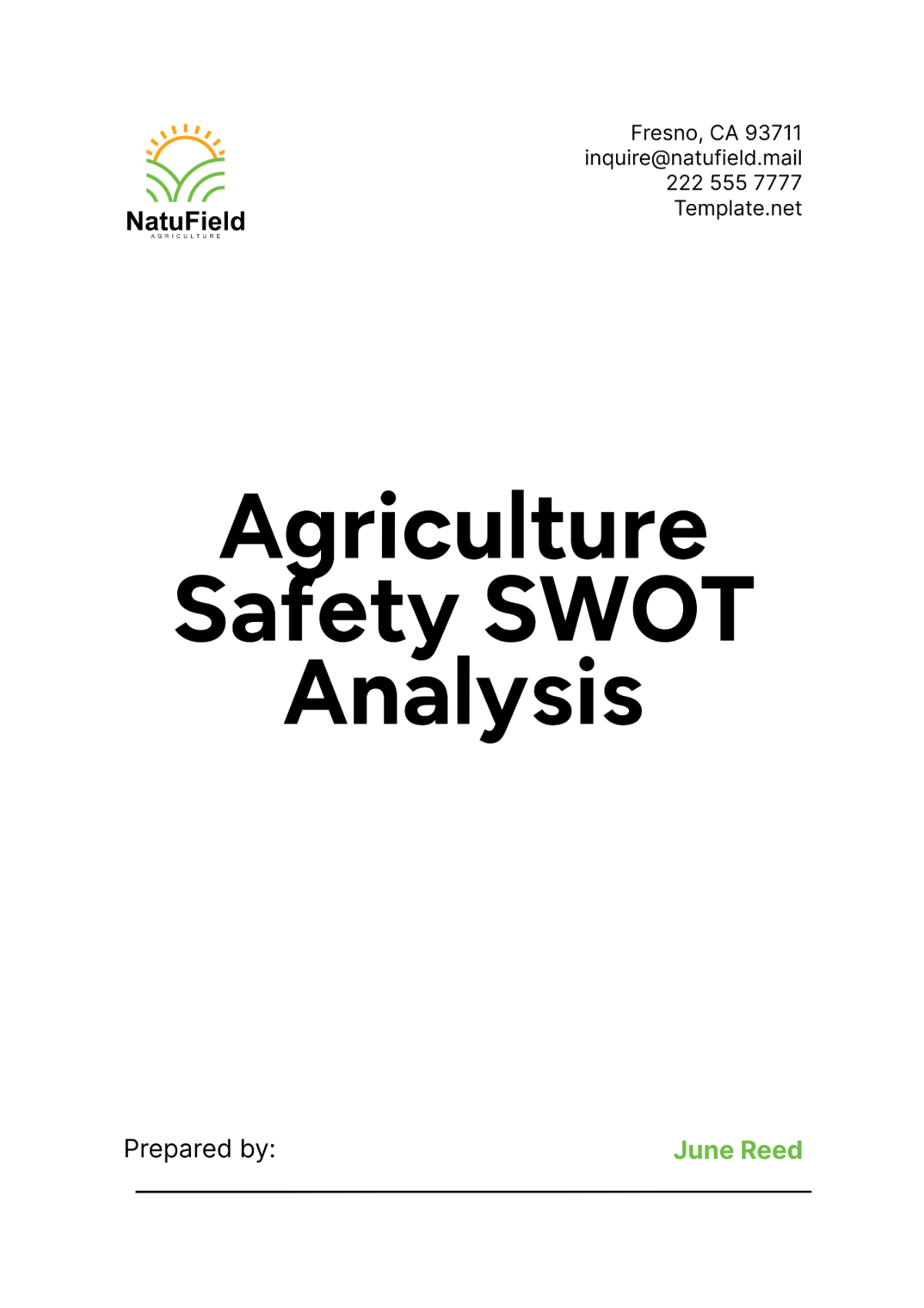
- 100% Customizable, free editor
- Access 1 Million+ Templates, photo’s & graphics
- Download or share as a template
- Click and replace photos, graphics, text, backgrounds
- Resize, crop, AI write & more
- Access advanced editor
Identify strengths, weaknesses, opportunities, and threats with our Agriculture Safety SWOT Analysis Template! Available on Template.net, it offers customizable sections to reflect your unique business branding. Fully editable, this template allows precise adjustments to suit your safety protocols. The advanced AI Editor Tool enhances the process, ensuring an accurate analysis!
You may also like
Agriculture Safety SWOT Analysis
I. Introduction
Agricultural safety is a critical aspect of [Your Company Name]'s operations. Ensuring the safety of our workforce, equipment, and environment not only safeguards our employees but also enhances productivity and sustainability. This analysis aims to identify the strengths, weaknesses, opportunities, and threats related to safety within our agricultural practices. By understanding these factors, we can implement targeted strategies to maintain and improve our safety standards.
In this comprehensive SWOT analysis, we will explore various elements of our safety protocols and procedures. The findings from this analysis will provide valuable insights into areas where we excel and highlight opportunities for improvement. Additionally, identifying potential threats will help us develop proactive measures to mitigate risks.
II. Methodology
A. Data Collection
Surveys and Questionnaires: We distributed surveys and questionnaires to our employees to gather their perspectives on safety practices. This provided us with firsthand accounts of safety issues and strengths within our operations.
Safety Audits: Conducted comprehensive safety audits across all our facilities. These audits assessed compliance with safety regulations and identified potential hazards.
Incident Reports Analysis: Analyzed past incident reports to identify common safety issues and trends. This helped in understanding the root causes of accidents and near-misses.
B. Data Analysis
Statistical Analysis: Employed statistical tools to analyze the collected data. This included identifying patterns, trends, and correlations in safety incidents and compliance levels.
Comparative Analysis: Compared our safety performance with industry benchmarks. This provided a broader perspective on where we stand relative to our peers.
Root Cause Analysis: Conducted root cause analysis on identified safety issues to determine underlying factors. This helped in developing targeted recommendations.
C. Stakeholder Consultation
Employee Interviews: Conducted interviews with employees at various levels to gain deeper insights into safety practices and concerns. These interviews provided qualitative data to complement our quantitative findings.
Consultation with Safety Experts: Engaged external safety experts to review our practices and provide an objective assessment. Their feedback was instrumental in validating our findings.
Feedback Sessions: Held feedback sessions with key stakeholders, including management and safety officers, to discuss preliminary findings and gather additional input.
III. Strengths
A. Strong Safety Culture
Employee Awareness: Our workforce demonstrates a high level of awareness and commitment to safety protocols. Regular training sessions and safety drills have ingrained safety into our company culture.
Management Commitment: Senior management actively supports and prioritizes safety initiatives. This top-down approach ensures that safety remains a key focus across all operations.
Proactive Measures: We have implemented numerous proactive safety measures, such as regular equipment maintenance and hazard assessments, to prevent accidents before they occur.
B. Comprehensive Training Programs
Ongoing Education: Employees receive continuous education on safety practices. This includes regular refresher courses to keep everyone updated on the latest safety protocols.
Specialized Training: We offer specialized training programs tailored to specific roles and equipment. This ensures that employees have the necessary skills and knowledge to operate safely.
Safety Certifications: Many of our employees hold recognized safety certifications. These certifications validate their expertise and commitment to maintaining a safe working environment.
C. Advanced Safety Equipment
Modern Machinery: Our investment in modern, safety-enhanced machinery reduces the risk of accidents. These machines come equipped with advanced safety features and automation capabilities.
Protective Gear: We provide high-quality protective gear to all employees. This includes personal protective equipment (PPE) such as helmets, gloves, and safety goggles.
Safety Technology: Utilized advanced safety technologies, such as GPS tracking and remote monitoring, to enhance safety oversight and response capabilities.
IV. Weaknesses
A. Inconsistent Safety Compliance
Varying Adherence Levels: While many employees follow safety protocols diligently, there are inconsistencies in adherence across different teams and shifts. This variability increases the risk of accidents.
Complex Regulations: The complexity of safety regulations can lead to misunderstandings and non-compliance. Employees may find it challenging to stay updated with the latest rules and requirements.
Documentation Gaps: There are gaps in safety documentation and record-keeping. Incomplete records make it difficult to track compliance and identify recurring safety issues.
B. Limited Safety Resources
Insufficient Staffing: Our safety team is currently understaffed, limiting our ability to conduct regular inspections and audits. This staffing shortfall hampers proactive safety management.
Budget Constraints: Financial constraints have restricted our ability to invest in new safety technologies and equipment. This affects our capacity to implement the latest safety advancements.
Training Limitations: Due to budget and time constraints, not all employees receive comprehensive safety training. This lack of training leaves certain employees less prepared to handle safety risks.
C. Hazardous Working Conditions
Exposure to Chemicals: Employees in certain roles are exposed to hazardous chemicals. Inadequate protective measures can lead to health risks and safety incidents.
Manual Labor Risks: The nature of agricultural work involves significant manual labor, which increases the risk of injuries such as strains and sprains. Ergonomic improvements are needed to mitigate these risks.
Weather-Related Hazards: Adverse weather conditions can create unsafe working environments. Employees working outdoors face risks such as heat stress, hypothermia, and lightning strikes.
V. Opportunities
A. Technological Advancements
Automation and Robotics: Adopting automation and robotics can significantly enhance safety by reducing manual labor and minimizing human error. These technologies can perform hazardous tasks with precision and efficiency.
Wearable Safety Devices: Invest in wearable safety devices that monitor employee health and safety in real-time. These devices can detect signs of fatigue, monitor vital signs, and alert employees to potential hazards.
Drones for Surveillance: Utilize drones for aerial surveillance of large agricultural fields. Drones can quickly identify safety hazards, monitor compliance, and assist in emergency response efforts.
B. Enhanced Training Programs
E-Learning Platforms: Develop e-learning platforms to provide flexible and accessible safety training. Online courses can cover a wide range of topics and allow employees to learn at their own pace.
Virtual Reality Simulations: Implement virtual reality (VR) simulations for hands-on safety training. VR technology can create realistic scenarios that prepare employees for real-world situations.
Collaboration with Educational Institutions: Partner with agricultural colleges and universities to develop advanced safety training programs. These collaborations can bring in fresh perspectives and cutting-edge research.
C. Strengthening Safety Culture
Safety Champions Program: Establish a Safety Champions program where employees are recognized and rewarded for exemplary safety practices. This initiative can motivate others to prioritize safety.
Regular Safety Drills: Conduct regular safety drills to reinforce protocols and ensure employees are well-prepared for emergencies. These drills can include fire evacuations, chemical spill responses, and first aid exercises.
Feedback Mechanisms: Create anonymous feedback mechanisms for employees to report safety concerns without fear of retaliation. This can lead to timely identification and resolution of safety issues.
VI. Threats
A. Regulatory Changes
Stringent Regulations: Potential changes in safety regulations can impose stricter compliance requirements. Adapting to these changes may require significant investments in training and equipment.
Fines and Penalties: Non-compliance with evolving regulations can result in hefty fines and penalties. These financial repercussions can strain our resources and impact profitability.
Inspection Frequency: Increased frequency of regulatory inspections can disrupt operations and place additional pressure on our safety management systems.
B. Environmental Hazards
Natural Disasters: Natural disasters such as floods, hurricanes, and earthquakes pose significant threats to agricultural safety. Preparing for and responding to these events require comprehensive emergency plans.
Pest Infestations: Pest infestations can lead to crop damage and create unsafe working conditions. Effective pest management strategies are essential to mitigate these risks.
Climate Change: Climate change can exacerbate weather-related hazards and affect the overall safety of agricultural operations. Adapting to changing climate conditions is crucial for long-term safety.
C. Workforce Challenges
High Turnover Rates: High employee turnover rates can disrupt safety training and create gaps in safety knowledge. Ensuring continuity in safety practices is challenging with a transient workforce.
Aging Workforce: An aging workforce is more susceptible to injuries and health issues. Implementing ergonomic improvements and health support programs is necessary to protect older employees.
Language Barriers: Language barriers among a diverse workforce can hinder effective communication of safety protocols. Multilingual training materials and translation services can address this issue.
VII. Safety Performance Analysis
The following chart and table summarize the key safety performance indicators for [Your Company Name] over the past year:
Indicator | Target | Actual | Variance |
---|---|---|---|
Incident Rate | 2.0% | 1.5% | -0.5% |
Compliance Rate | 100% | 95% | -5% |
Training Completion Rate | 100% | 85% | -15% |
Safety Audit Score | 90% | 88% | -2% |
Employee Feedback Satisfaction | 80% | 75% | -5% |
A. Incident Rate
The incident rate measures the number of safety incidents relative to the total workforce. Our target was set at 2.0%, and we achieved an actual rate of 1.5%, indicating a lower-than-expected incidence of safety events. This positive outcome reflects the effectiveness of our current safety protocols and proactive measures.
However, it is essential to continue monitoring this indicator closely. While the current rate is favorable, maintaining or further reducing it requires ongoing commitment to safety training, equipment maintenance, and hazard prevention strategies.
B. Compliance Rate
Our compliance rate target is 100%, representing full adherence to safety regulations and standards. The actual compliance rate of 95% indicates a slight shortfall. This variance highlights areas where compliance can be improved through better training, clearer communication of regulations, and more rigorous enforcement of safety policies.
Improving our compliance rate is crucial for avoiding penalties and ensuring the well-being of our employees. Regular audits and spot checks can help identify non-compliance issues promptly and address them effectively.
C. Training Completion Rate
The training completion rate indicates the percentage of employees who have completed mandatory safety training. Our target was 100%, but the actual rate was 85%. This shortfall suggests that some employees may not have received or completed the necessary training, potentially putting them at risk.
To address this, we need to implement stricter tracking and follow-up mechanisms to ensure all employees complete their training on time. Additionally, providing flexible training options and making training more accessible can help improve completion rates.
D. Safety Audit Score
The safety audit score measures the effectiveness of our safety management systems based on periodic audits. Our target was 90%, and the actual score was 88%, indicating a minor variance. While this score is relatively high, there is room for improvement.
Enhancing our audit processes and addressing identified gaps can help us achieve higher scores. Regular internal audits and external reviews can provide valuable feedback and drive continuous improvement in our safety practices.
E. Employee Feedback Satisfaction
Employee feedback satisfaction measures the satisfaction level of employees regarding safety practices and conditions. Our target was 80%, and the actual satisfaction rate was 75%. This variance suggests some dissatisfaction among employees, which could be due to various factors such as perceived safety risks, lack of communication, or insufficient support.
Addressing employee concerns through regular feedback sessions, open communication channels, and prompt resolution of safety issues can help improve satisfaction levels. Engaging employees in safety initiatives and recognizing their contributions can also enhance overall satisfaction and commitment to safety.
VIII. Recommendations
A. Enhance Safety Training Programs
Increase Training Accessibility: Develop flexible training options, including online courses and on-site sessions, to ensure all employees can complete their training regardless of their schedules.
Regular Refresher Courses: Implement mandatory refresher courses to reinforce safety protocols and update employees on new regulations and practices.
Multilingual Training Materials: Provide training materials in multiple languages to overcome language barriers and ensure all employees understand safety requirements.
B. Strengthen Compliance Measures
Regular Audits and Inspections: Conduct regular internal and external audits to monitor compliance and identify areas for improvement. Implement corrective actions promptly to address any non-compliance issues.
Clear Communication of Regulations: Ensure that safety regulations and policies are clearly communicated to all employees. Use visual aids, posters, and digital platforms to reinforce key messages.
Incentivize Compliance: Introduce incentives for teams and individuals who consistently adhere to safety regulations. Recognize and reward compliance to encourage a culture of safety.
C. Invest in Safety Equipment and Technology
Upgrade Protective Gear: Provide employees with the latest personal protective equipment (PPE) to enhance their safety. Regularly review and update PPE to meet evolving safety standards.
Adopt Safety Technologies: Invest in advanced safety technologies such as wearable devices, drones, and automated monitoring systems to enhance safety oversight and response capabilities.
Modernize Machinery: Upgrade outdated machinery with modern, safety-enhanced equipment to reduce the risk of accidents and improve operational efficiency.
D. Improve Hazard Management
Implement Ergonomic Solutions: Introduce ergonomic improvements to reduce the risk of injuries related to manual labor. This includes adjustable workstations, proper lifting techniques, and ergonomic tools.
Strengthen Chemical Safety Protocols: Enhance safety measures for handling hazardous chemicals. Provide additional training on chemical safety and ensure proper storage and disposal practices.
Prepare for Weather-Related Hazards: Develop comprehensive plans to address weather-related hazards. This includes providing appropriate protective gear, training on weather-related risks, and establishing emergency response protocols.
E. Foster a Safety-First Culture
Safety Champions Program: Establish a program to recognize and reward employees who demonstrate exemplary safety practices. This can motivate others to prioritize safety and contribute to a safer work environment.
Open Feedback Channels: Create anonymous feedback mechanisms for employees to report safety concerns without fear of retaliation. Regularly review and act on feedback to address safety issues.
Regular Safety Drills: Conduct regular safety drills to ensure employees are prepared for emergencies. Include scenarios such as fire evacuations, chemical spills, and first aid exercises in the drills.
IX. Conclusion
[Your Company Name] has demonstrated significant strengths in maintaining a strong safety culture, providing comprehensive training, and investing in advanced safety equipment. However, there are areas that require improvement, such as enhancing compliance measures, improving training completion rates, and addressing hazardous working conditions.
By implementing the recommendations outlined in this report, [Your Company Name] can further strengthen its safety practices and ensure a safer working environment for all employees. Continued commitment to safety will not only protect our workforce but also enhance our operational efficiency and sustainability in the long run.