Free Agriculture Safety Training Protocol
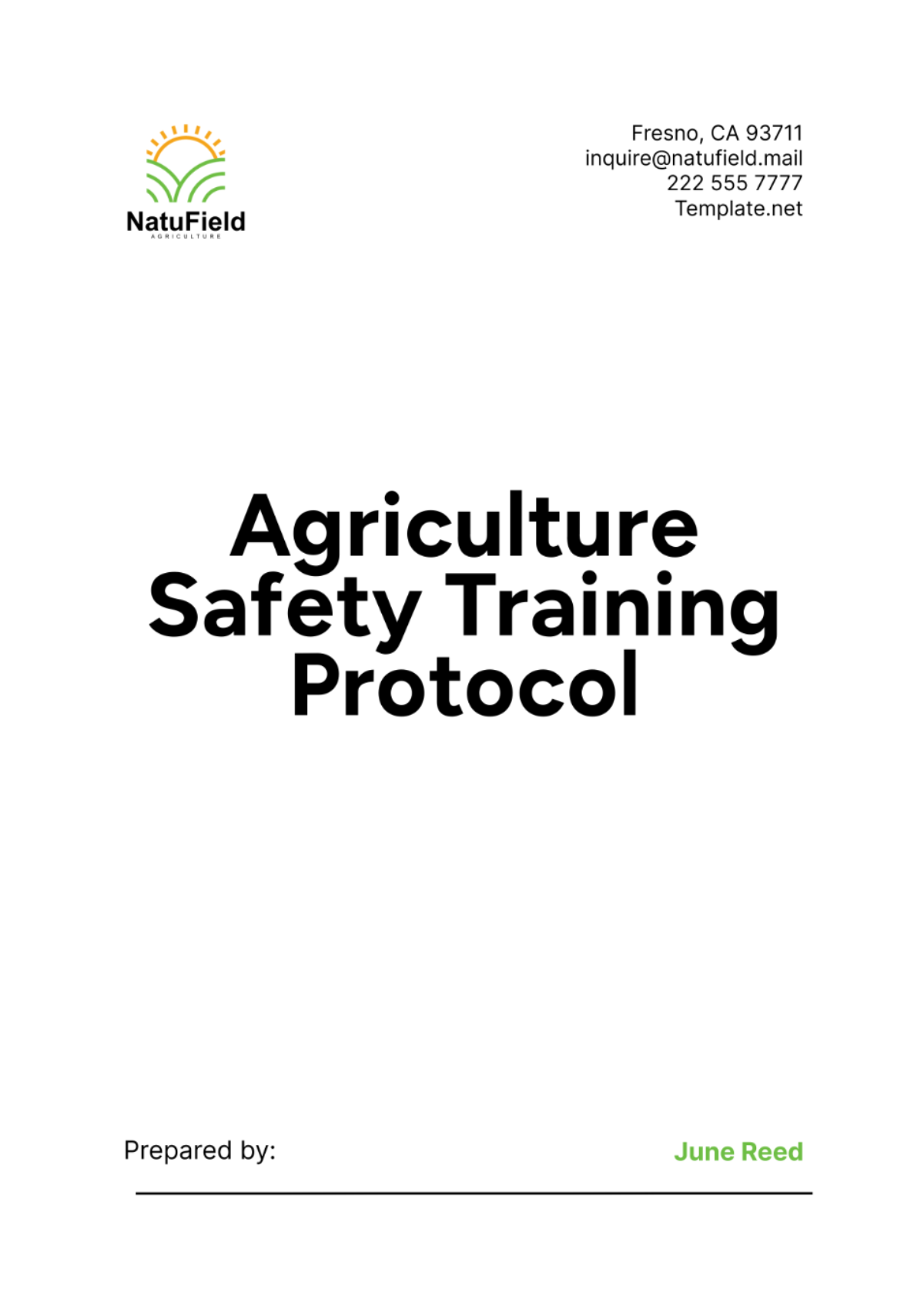
- 100% Customizable, free editor
- Access 1 Million+ Templates, photo’s & graphics
- Download or share as a template
- Click and replace photos, graphics, text, backgrounds
- Resize, crop, AI write & more
- Access advanced editor
Improve your farm's safety standards with the Agriculture Safety Training Protocol Template from Template.net. This fully editable and customizable template ensures comprehensive safety training for all agricultural operations. Utilize the AI Editor Tool to easily tailor the protocol to your specific needs, ensuring a safer, more compliant workplace. Access and adapt with ease today.
You may also like
Agriculture Safety Training Protocol
I. Introduction
A. Purpose of the Safety Training Protocol
The purpose of this Safety Training Protocol is to provide a structured approach to identifying, managing, and mitigating risks associated with agricultural operations. By implementing this protocol, we aim to protect the health and safety of our employees, contractors, and visitors. The protocol serves as a guideline for safe practices and emergency response procedures to ensure a safe working environment.
B. Objectives of the Training
The primary objectives of the training are to raise awareness of potential workplace hazards and to equip employees with the knowledge and skills necessary to perform their tasks safely. The training aims to reduce the incidence of workplace injuries and illnesses by promoting a culture of safety and compliance. Additionally, the training seeks to ensure that all employees are familiar with emergency procedures and know how to respond effectively in case of an incident.
C. Scope and Applicability
This safety training protocol applies to all employees, contractors, and visitors involved in any aspect of agricultural operations on the farm. It covers a wide range of activities, from machinery operation and chemical handling to fieldwork and emergency response. The protocol is designed to be adaptable to various agricultural settings and is regularly updated to reflect new regulations, technologies, and best practices.
II. Regulatory Compliance
A. Overview of Relevant Safety Regulations
Occupational Safety and Health Administration (OSHA) Standards
OSHA standards are designed to ensure safe and healthful working conditions by setting and enforcing standards and providing training, outreach, education, and assistance. Relevant OSHA standards for agriculture include regulations on machine guarding, fall protection, and hazard communication. Compliance with these standards is mandatory and helps prevent workplace injuries and fatalities.
Environmental Protection Agency (EPA) Regulations
EPA regulations focus on protecting human health and the environment from the potential hazards of pesticides and other chemicals used in agriculture. These regulations include guidelines for the safe use, storage, and disposal of hazardous substances. Compliance with EPA regulations is essential to prevent environmental contamination and ensure the safety of workers handling these chemicals.
B. Legal Requirements for Safety Training
Safety training must be conducted in accordance with federal, state, and local regulations. This includes providing initial training for new hires, as well as regular refresher courses for all employees. Training records must be maintained to demonstrate compliance and to ensure that all employees have received the necessary instruction to perform their jobs safely.
III. Risk Assessment and Hazard Identification
A. Methods for Identifying Hazards
Site Inspections
Regular site inspections are essential for identifying potential hazards in the workplace. These inspections should be conducted by trained personnel who can recognize unsafe conditions and practices. Inspection findings should be documented, and corrective actions should be implemented promptly to mitigate identified risks.
Job Safety Analysis (JSA)
A Job Safety Analysis involves breaking down a job into its individual tasks and identifying the hazards associated with each step. This process helps in developing safe work procedures and identifying the necessary controls to prevent accidents. JSAs should be reviewed and updated regularly to reflect any changes in job tasks or equipment.
B. Risk Assessment Techniques
Hazard Ranking Systems
Hazard ranking systems prioritize risks based on their severity and likelihood of occurrence. This helps in focusing resources on the most significant hazards. By ranking hazards, safety managers can develop targeted strategies to reduce the highest risks first, ensuring a more effective safety management process.
Risk Mitigation Strategies
Risk mitigation strategies involve implementing controls to reduce the likelihood and impact of identified hazards. These strategies can include engineering controls, such as machine guards, administrative controls, such as training and work procedures, and the use of personal protective equipment (PPE). Regular monitoring and evaluation of these controls are necessary to ensure their effectiveness.
IV. Safety Policies and Procedures
A. General Safety Policies
Code of Conduct
The code of conduct outlines the expected behavior and responsibilities of all employees to maintain a safe and respectful workplace. This includes following all safety rules, reporting unsafe conditions, and participating in safety training. Adherence to the code of conduct is mandatory, and violations may result in disciplinary actions.
Reporting Unsafe Conditions
Employees are encouraged to report any unsafe conditions or practices they observe in the workplace. A clear reporting process should be established, and employees should be assured that their reports will be taken seriously and addressed promptly. Reporting unsafe conditions helps in preventing accidents and improving overall workplace safety.
B. Specific Safety Procedures
Equipment Operation
Safe operation of equipment is critical to prevent accidents and injuries. Employees must be trained and authorized to operate machinery, and they must follow manufacturer instructions and safety guidelines. Pre-operation checks are essential to ensure that equipment is in good working condition and safe to use.
Chemical Handling
Proper procedures for handling, mixing, and applying chemicals are crucial to prevent exposure and contamination. Employees must use appropriate PPE and follow safety data sheets (SDS) for each chemical. Safe storage and disposal practices must also be adhered to, ensuring that chemicals are kept in secure, labeled containers and disposed of according to regulations.
Field Work Safety
Fieldwork involves various hazards such as uneven terrain, exposure to extreme weather, and encounters with wildlife. Employees must be aware of these hazards and take necessary precautions, such as wearing appropriate footwear, staying hydrated, and using sun protection. Regular safety briefings and field inspections help ensure that safe practices are followed.
V. Personal Protective Equipment (PPE)
A. Types of PPE Required
Head Protection
Head protection, such as hard hats, is required in areas where there is a risk of falling objects or head injuries. Hard hats must meet industry standards and be inspected regularly for damage. Employees must wear head protection at all times when working in designated areas.
Eye and Face Protection
Safety glasses or face shields are necessary when handling chemicals, operating machinery, or performing tasks that may result in flying debris. Eye and face protection must fit properly and be kept clean and free from scratches. Employees should be trained on when and how to use this equipment correctly.
Hand Protection
Appropriate gloves must be worn to protect against cuts, abrasions, chemical exposure, and other hazards. Different types of gloves are needed for different tasks, and employees must select the right gloves for the job. Regular inspection and replacement of gloves are important to maintain their protective qualities.
Foot Protection
Sturdy, slip-resistant boots are required to protect against foot injuries from heavy objects, sharp tools, and uneven surfaces. Boots should provide good ankle support and be made of materials suitable for the specific work environment. Employees must ensure their footwear is in good condition and replace it when worn out.
B. Proper Use and Maintenance of PPE
Inspection and Fit Testing
PPE must be inspected before each use to ensure it is in good condition and functioning properly. Fit testing, particularly for respirators, is essential to ensure a proper seal and effective protection. Regular inspections help identify any damage or wear that could compromise safety.
Cleaning and Storage
PPE should be cleaned after use according to manufacturer instructions to prevent contamination and maintain hygiene. Proper storage in designated areas protects PPE from damage and prolongs its lifespan. Employees must be trained on proper cleaning and storage procedures to ensure PPE remains effective.
VI. Emergency Response Plan
A. Emergency Procedures
Fire Response
In case of fire, employees must know how to activate the nearest alarm, evacuate the area safely, and call emergency services. Fire extinguishers should be readily accessible, and employees should be trained in their use. Regular fire drills help ensure everyone knows their role in an emergency.
Medical Emergencies
For medical emergencies, employees should provide first aid if trained, call emergency services, and report the incident to a supervisor. Knowing the location of first aid kits and emergency contact numbers is crucial. Quick and effective response can save lives and reduce the severity of injuries.
Chemical Spills
In the event of a chemical spill, employees should use spill kits, evacuate the area if necessary, and report the incident immediately. Proper containment and cleanup procedures must be followed to prevent environmental contamination and exposure. Training on spill response is essential for all employees handling chemicals.
B. Emergency Contact Information
Internal Contacts
Internal emergency contacts include the Farm Manager and Safety Officer, who are responsible for coordinating emergency response efforts. Contact information for these individuals should be readily available to all employees. Clear communication channels ensure timely and effective response to emergencies.
External Emergency Services
External emergency services include the local fire department, medical services, and environmental agencies. Employees should be familiar with the contact numbers for these services and know when to call them. Collaboration with external services enhances overall emergency preparedness and response.
VII. First Aid and Medical Response
A. Basic First Aid Procedures
Employees should be trained in basic first aid procedures, including how to clean and bandage wounds, apply cold packs for sprains, and recognize symptoms of serious conditions such as heat stroke or allergic reactions. Providing immediate care can prevent minor injuries from becoming more serious.
B. Reporting Injuries and Seeking Medical Attention
All injuries, no matter how minor, must be reported to a supervisor immediately. This ensures that appropriate medical attention can be provided and that the incident is documented for future reference. Prompt reporting and treatment help in preventing complications and ensuring a safe workplace.
C. Location and Use of First Aid Kits
First aid kits should be located in easily accessible areas such as the main office, workshop, and field stations. Employees must be trained in the contents and use of first aid kits. Regular checks and replenishment of supplies ensure that kits are always ready for use in an emergency.
VIII. Machinery and Equipment Safety
A. Safe Operation of Machinery
Tractors
Operators must receive thorough training on tractor operation, including starting, stopping, and maneuvering techniques. Regular maintenance checks and adherence to manufacturer guidelines help ensure safe operation. Safety features such as roll-over protective structures (ROPS) must always be used.
Harvesters
Harvesters involve complex mechanisms that require specialized training for safe operation. Operators must be aware of potential hazards such as moving parts and entanglement risks. Routine inspections and maintenance are crucial to prevent accidents and ensure the machinery functions correctly.
Irrigation Systems
Safe operation of irrigation systems includes understanding the electrical components and water pressure controls. Regular inspections for leaks, blockages, and electrical faults are necessary to maintain safe and efficient operation. Proper training on system operation and emergency shut-off procedures is essential.
B. Regular Maintenance and Inspections
Maintenance Schedules
Adhering to maintenance schedules is critical to the safe operation of machinery and equipment. Scheduled maintenance includes routine checks, lubrication, and replacement of worn parts. Keeping detailed maintenance records helps in tracking performance and identifying recurring issues.
Inspection Checklists
Inspection checklists ensure that all safety-critical components are regularly checked for proper functioning. These checklists should cover aspects such as brakes, steering, safety guards, and fluid levels. Regular inspections help in early identification of potential problems and prevent equipment failures.
C. Lockout/Tagout Procedures
Lockout/tagout procedures are essential for ensuring the safety of employees during maintenance and repair work. These procedures involve isolating energy sources and securing machinery to prevent accidental start-up. Proper training on lockout/tagout procedures helps in preventing serious injuries and fatalities.
IX. Chemical Safety
A. Safe Storage of Chemicals
Proper storage of chemicals is essential to prevent leaks, spills, and contamination. Chemicals must be stored in labeled, secure containers and kept in designated areas away from incompatible substances. Regular inspections of storage areas ensure compliance with safety regulations and help identify potential hazards.
B. Safe Handling Procedures
Employees handling chemicals must follow specific procedures to minimize exposure and prevent accidents. This includes using appropriate personal protective equipment (PPE), understanding safety data sheets (SDS), and following proper mixing and application guidelines. Training on handling procedures is crucial for maintaining a safe work environment.
C. Emergency Response to Chemical Exposure
In the event of chemical exposure, employees must know how to use emergency eyewash stations and showers, seek medical attention, and report the incident immediately. Quick and effective response can mitigate the effects of exposure and prevent serious health issues. Regular drills and training ensure preparedness for such emergencies.
X. Training Programs
A. Initial Training for New Employees
New employees must undergo comprehensive safety training before starting their duties. This training includes an overview of workplace hazards, safe work practices, and emergency procedures. Ensuring that new hires are well-informed and equipped with the necessary skills helps in preventing accidents and promoting a culture of safety.
B. Regular Refresher Courses
Regular refresher courses are necessary to reinforce safety knowledge and keep employees updated on new regulations and practices. These courses should be scheduled periodically and cover topics such as hazard recognition, PPE usage, and emergency response. Continuous training helps maintain high safety standards and prevents complacency.
C. Specialized Training for High-Risk Tasks
High-risk tasks, such as operating heavy machinery or handling hazardous chemicals, require specialized training. This training focuses on the specific hazards associated with these tasks and the safety measures needed to perform them safely. Providing targeted training ensures that employees are well-prepared to handle high-risk activities.
XI. Monitoring and Evaluation
A. Incident Reporting and Investigation
All incidents, including near-misses, must be reported and investigated to identify their root causes. This process involves documenting the incident, interviewing witnesses, and analyzing contributing factors. Thorough investigations help in developing corrective actions to prevent recurrence and improve overall safety.
B. Safety Audits and Inspections
Regular safety audits and inspections are essential for identifying potential hazards and ensuring compliance with safety protocols. These audits should be conducted by trained personnel and cover all aspects of the workplace. Findings from audits are used to make necessary improvements and maintain a safe working environment.
C. Continuous Improvement Strategies
Continuous improvement strategies involve regularly reviewing and updating safety policies, procedures, and training programs. Feedback from employees, incident reports, and audit findings are used to identify areas for improvement. Implementing these strategies helps in creating a proactive safety culture and reducing workplace risks.
XII. Documentation and Record Keeping
A. Training Records
Maintaining accurate training records is essential for tracking employee participation in safety programs and ensuring compliance with regulations. These records should include details of training sessions, attendance, and topics covered. Proper documentation helps in verifying that all employees have received the necessary training.
B. Incident and Accident Reports
Detailed incident and accident reports are crucial for understanding the circumstances leading to workplace injuries and implementing preventive measures. These reports should include information about the incident, the individuals involved, and the corrective actions taken. Accurate reporting helps in identifying trends and improving safety protocols.
C. Safety Audit Reports
Safety audit reports provide a comprehensive overview of the workplace's compliance with safety regulations and protocols. These reports should document findings, recommendations, and corrective actions. Regular review of audit reports helps in maintaining high safety standards and addressing any identified issues promptly.
XIII. Employee Involvement
A. Safety Committees
Establishing safety committees encourages employee involvement in safety management and fosters a collaborative approach to hazard identification and mitigation. These committees should include representatives from different departments and meet regularly to discuss safety concerns and recommend improvements. Active participation in safety committees enhances overall workplace safety.
B. Suggestion Programs
Encouraging employees to contribute safety suggestions helps in identifying potential hazards and improving safety practices. Suggestion programs should provide a structured process for submitting and reviewing ideas, with recognition and rewards for valuable contributions. Involving employees in safety initiatives promotes a culture of continuous improvement.
C. Safety Communication Channels
Effective communication channels ensure that safety information is disseminated promptly and clearly to all employees. This includes regular safety meetings, bulletin boards, and digital platforms. Providing multiple channels for communication helps in keeping employees informed and engaged in safety efforts.
XIV. Management Responsibilities
A. Role of Management in Safety
Management plays a critical role in establishing and maintaining a safe workplace by setting safety policies, providing resources, and leading by example. Management's commitment to safety demonstrates its importance and encourages employees to prioritize safe work practices. Active involvement of management in safety initiatives enhances overall safety culture.
B. Allocation of Resources
Allocating adequate resources for safety programs, including training, equipment, and personnel, is essential for their effectiveness. Management must ensure that sufficient funding and support are available to implement safety measures and maintain compliance with regulations. Proper resource allocation helps in sustaining long-term safety improvements.
C. Accountability and Enforcement
Holding employees and supervisors accountable for adhering to safety protocols is crucial for maintaining high safety standards. This includes implementing disciplinary actions for non-compliance and recognizing exemplary safety performance. Establishing clear accountability and enforcement mechanisms ensures that safety remains a top priority.
XV. Review and Update of Protocol
A. Periodic Review Schedule
Regular reviews of the safety training protocol ensure that it remains current and effective. These reviews should be scheduled annually or following significant changes in operations or regulations. Periodic reviews help in identifying areas for improvement and incorporating new best practices.
B. Incorporating Feedback and Improvements
Feedback from employees, safety committees, and audits should be used to update the protocol and address any identified issues. Continuous improvement relies on incorporating practical suggestions and lessons learned from past incidents. Engaging employees in the review process enhances the relevance and effectiveness of the protocol.
C. Communication of Updates
Communicating updates to the safety training protocol is essential for ensuring that all employees are aware of changes and understand their implications. This can be achieved through training sessions, meetings, and written communications. Clear communication helps in maintaining compliance and reinforcing the importance of safety practices.