Free Six Sigma Methodology
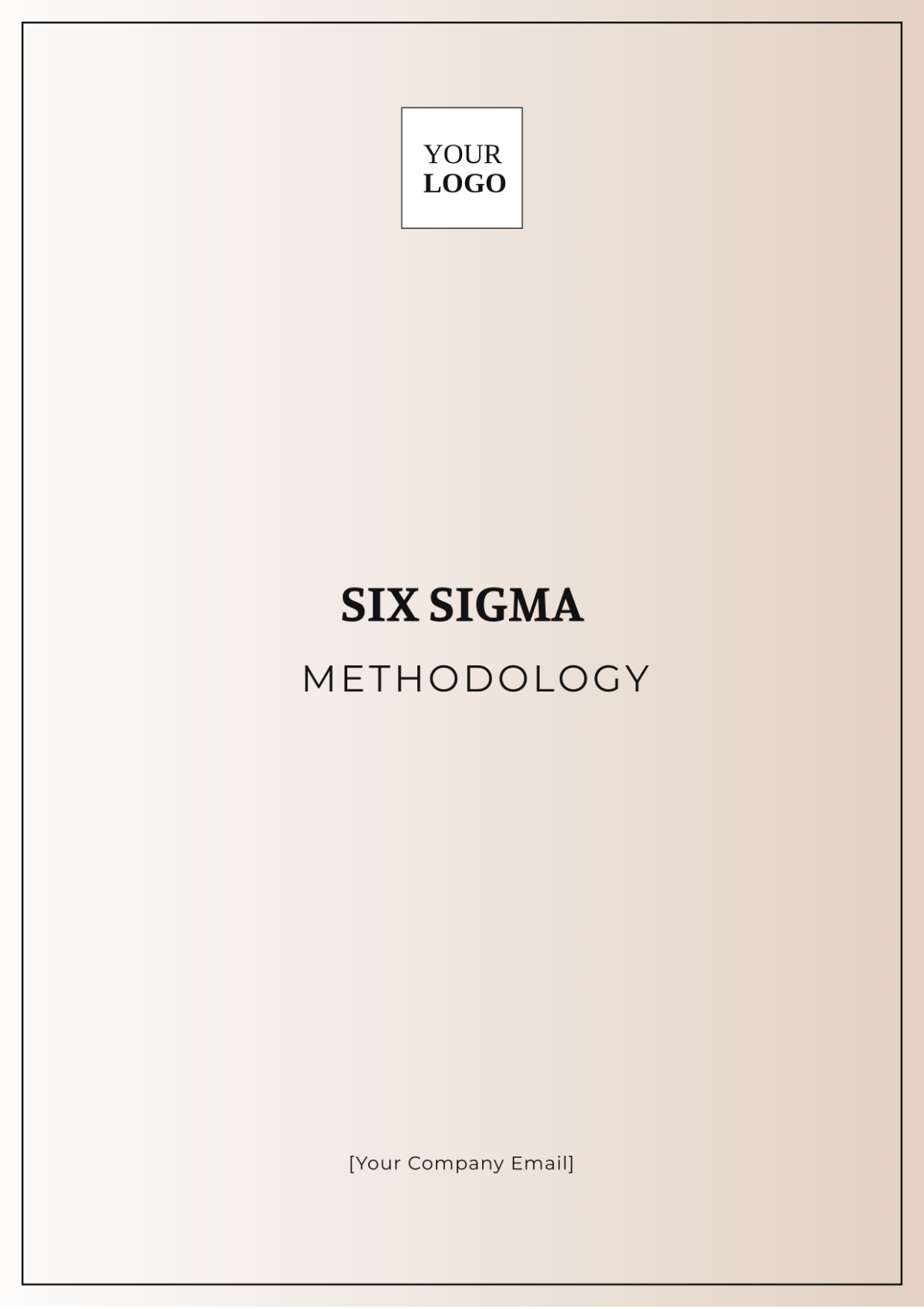
- 100% Customizable, free editor
- Access 1 Million+ Templates, photo’s & graphics
- Download or share as a template
- Click and replace photos, graphics, text, backgrounds
- Resize, crop, AI write & more
- Access advanced editor
Achieve quality excellence with Template.net's Six Sigma Methodology Template. Customizable and editable, this template is designed to help you implement Six Sigma practices effectively. Editable in our Ai Editor Tool, it allows for easy adaptation to your specific project goals, ensuring high-quality outcomes.
You may also like
Six Sigma Methodology
Introduction
Six Sigma is a structured approach for improving processes and eliminating defects. Developed by engineer Bill Smith at Motorola in 1986, Six Sigma aims to enhance operational performance through data-driven decisions and statistical analysis. It focuses on reducing variability and defects in both manufacturing and service processes, striving for near-perfect quality levels. For example, achieving a Six Sigma level means having fewer than 3.4 defects per million opportunities, which signifies a high level of process efficiency and customer satisfaction.
Define Phase
The Define phase sets the foundation for the Six Sigma project by clarifying the problem and outlining the project framework.
Project Charter
Problem Statement: High defect rates in the assembly process are leading to increased rework and customer complaints.
Business Case: Reducing defects by 30% will decrease rework costs by $150,000 annually and improve customer satisfaction scores by 15%.
Goal Statement: Achieve a defect rate reduction from 5% to 1% within six months.
Team Members and Roles: Project Manager: Sarah Jones, Process Engineer: John Smith, Data Analyst: Maria Garcia.
Project Scope: Focus on the assembly line for product X; excludes packaging and shipping processes.
Timeline and Milestones: Define Phase Completion: 2 weeks; Measure Phase Start: 3 weeks from project initiation.
Voice of the Customer (VOC)
Customer Needs and Requirements: Customers expect 99.9% defect-free products.
Stakeholder Analysis: Key stakeholders include production managers, quality control teams, and end-users.
SIPOC Diagram
Suppliers: Component suppliers A and B.
Inputs: Raw materials, assembly components.
Process: Product assembly, quality inspection.
Outputs: Finished products, inspection reports.
Customers: Retailers, end-users.
Communication Plan
Stakeholder Engagement: Weekly project updates to all team members and bi-weekly reports to senior management.
Communication Strategies and Channels: Use of email newsletters, project management software, and team meetings.
Measure Phase
The Measure phase involves quantifying current process performance and identifying key variables.
Process Mapping
Current State Process Map: Flowchart showing each step from component arrival to final assembly.
Value Stream Map: Map highlighting value-adding and non-value-adding activities.
Data Collection Plan
Identify Key Metrics: Defect rates, cycle times, and process yield.
Data Collection Methods: Automated data logging, and manual inspections.
Sampling Techniques: Random sampling of 50 units per production batch.
Measurement System Analysis (MSA)
Gauge R&R: Testing measurement tools for consistency and accuracy.
Attribute Agreement Analysis: Evaluating different inspectors’ agreements on defect classification.
Baseline Performance
Descriptive Statistics: Mean defect rate of 4.5% with a standard deviation of 0.5%.
Process Capability Analysis: CpK of 1.2 indicates moderate process capability.
Analyze Phase
The Analyze phase focuses on identifying and validating the root causes of defects and opportunities for improvement.
Root Cause Analysis
Fishbone Diagram (Ishikawa): Diagram showing potential causes such as machine wear, operator error, and material defects.
5 Whys Analysis: Why are defects occurring? Because of improper machine settings. Why? Settings are not standardized. Why? No established protocol.
Hypothesis Testing
Formulate Hypotheses: Improper machine calibration is causing higher defect rates.
Conduct Tests: t-tests to compare defect rates with different calibration settings.
Value-Added Analysis
Identify Value-Added Steps: Steps directly involved in assembly and quality checking.
Identify Non-Value-Added Steps: Unnecessary waiting times between assembly and inspection.
Eliminate Waste: Streamline process to reduce waiting time.
Failure Mode and Effects Analysis (FMEA)
Potential Failure Modes: Machine breakdowns, incorrect settings.
Severity, Occurrence, and Detection Rankings: Severity: 8, Occurrence: 6, Detection: 4.
Risk Priority Number (RPN): RPN of 192 indicating high risk.
Improve Phase
The improvement phase involves developing and implementing solutions to address identified problems.
Solution Development
Brainstorming and Ideation: Generating ideas like machine recalibration, improved training, and process automation.
Selection and Prioritization of Solutions: Prioritize recalibration and training based on impact and feasibility.
Pilot Testing
Design Pilot Study: Test recalibration on one assembly line segment.
Implement Pilot Study: Apply new calibration procedures to the pilot segment.
Analyze Pilot Study Results: Monitor defect rates before and after implementation.
Implementation Plan
Detailed Action Plan: Step-by-step plan for full-scale implementation of recalibration procedures.
Resource Allocation: Assign technicians for recalibration and budget for training materials.
Timeline and Milestones: Full implementation in 3 months with progress reviews in 1 and 2 months.
Risk Mitigation
Identify Implementation Risks: Potential delays in training and resistance to change.
Develop Mitigation Strategies: Contingency plans for additional training sessions and stakeholder engagement.
Control Phase
The Control phase ensures the improvements are sustained and processes are standardized.
Control Plan
Monitoring Key Metrics: Regular tracking of defect rates and process performance.
Control Charts: X-bar and R charts for ongoing defect monitoring.
Documentation
Standard Operating Procedures (SOPs): Documented procedures for machine calibration and quality checks.
Process Documentation: Updated process maps and work instructions.
Training and Knowledge Transfer
Training Plans: Training programs for new procedures and equipment usage.
Knowledge Transfer Sessions: Workshops to transfer knowledge from the project team to operational staff.
Sustaining Improvements
Audit Plans: Regular audits to ensure adherence to new processes.
Continuous Improvement Strategies: Ongoing review meetings and suggestion programs for process enhancements.
Conclusion
The Six Sigma Methodology offers a rigorous framework for process improvement through the DMAIC phases. By leveraging data analysis and systematic problem-solving techniques, organizations can achieve significant performance improvements, reduce defects, and enhance overall quality. Through diligent application of the Six Sigma tools and methods, businesses can achieve operational excellence and exceed customer expectations.