Free Garment Production Outline Plan
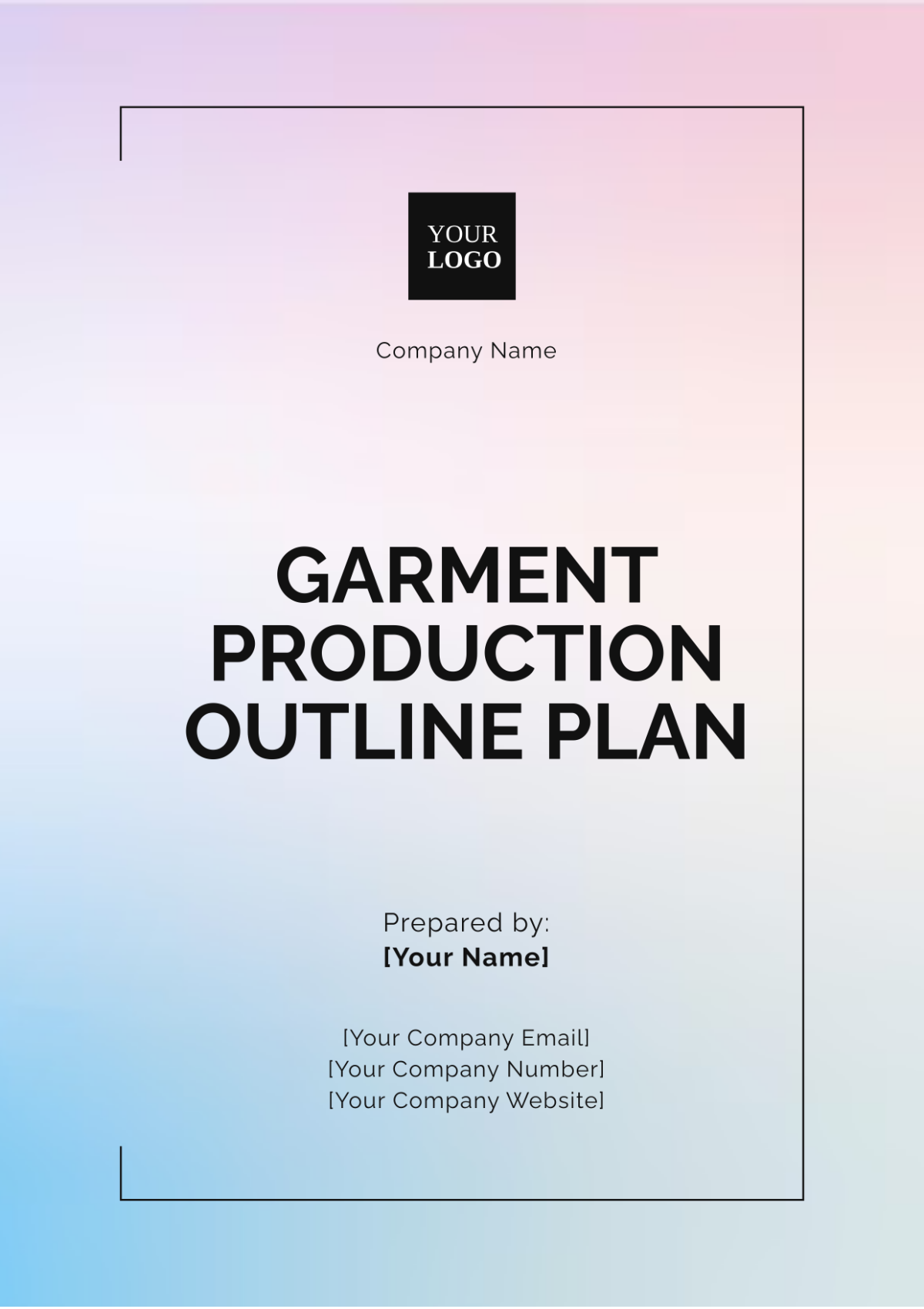
- 100% Customizable, free editor
- Access 1 Million+ Templates, photo’s & graphics
- Download or share as a template
- Click and replace photos, graphics, text, backgrounds
- Resize, crop, AI write & more
- Access advanced editor
Plan your garment production efficiently with the Garment Production Outline Plan Template from Template.net. This customizable and editable template covers all production phases, ensuring a smooth workflow. Easily make adjustments and tailor it to your needs, with full editing capabilities editable in our Ai Editor Tool for streamlined production management. Perfect for optimizing your garment production process.
You may also like
- Finance Plan
- Construction Plan
- Sales Plan
- Development Plan
- Career Plan
- Budget Plan
- HR Plan
- Education Plan
- Transition Plan
- Work Plan
- Training Plan
- Communication Plan
- Operation Plan
- Health And Safety Plan
- Strategy Plan
- Professional Development Plan
- Advertising Plan
- Risk Management Plan
- Restaurant Plan
- School Plan
- Nursing Home Patient Care Plan
- Nursing Care Plan
- Plan Event
- Startup Plan
- Social Media Plan
- Staffing Plan
- Annual Plan
- Content Plan
- Payment Plan
- Implementation Plan
- Hotel Plan
- Workout Plan
- Accounting Plan
- Campaign Plan
- Essay Plan
- 30 60 90 Day Plan
- Research Plan
- Recruitment Plan
- 90 Day Plan
- Quarterly Plan
- Emergency Plan
- 5 Year Plan
- Gym Plan
- Personal Plan
- IT and Software Plan
- Treatment Plan
- Real Estate Plan
- Law Firm Plan
- Healthcare Plan
- Improvement Plan
- Media Plan
- 5 Year Business Plan
- Learning Plan
- Marketing Campaign Plan
- Travel Agency Plan
- Cleaning Services Plan
- Interior Design Plan
- Performance Plan
- PR Plan
- Birth Plan
- Life Plan
- SEO Plan
- Disaster Recovery Plan
- Continuity Plan
- Launch Plan
- Legal Plan
- Behavior Plan
- Performance Improvement Plan
- Salon Plan
- Security Plan
- Security Management Plan
- Employee Development Plan
- Quality Plan
- Service Improvement Plan
- Growth Plan
- Incident Response Plan
- Basketball Plan
- Emergency Action Plan
- Product Launch Plan
- Spa Plan
- Employee Training Plan
- Data Analysis Plan
- Employee Action Plan
- Territory Plan
- Audit Plan
- Classroom Plan
- Activity Plan
- Parenting Plan
- Care Plan
- Project Execution Plan
- Exercise Plan
- Internship Plan
- Software Development Plan
- Continuous Improvement Plan
- Leave Plan
- 90 Day Sales Plan
- Advertising Agency Plan
- Employee Transition Plan
- Smart Action Plan
- Workplace Safety Plan
- Behavior Change Plan
- Contingency Plan
- Continuity of Operations Plan
- Health Plan
- Quality Control Plan
- Self Plan
- Sports Development Plan
- Change Management Plan
- Ecommerce Plan
- Personal Financial Plan
- Process Improvement Plan
- 30-60-90 Day Sales Plan
- Crisis Management Plan
- Engagement Plan
- Execution Plan
- Pandemic Plan
- Quality Assurance Plan
- Service Continuity Plan
- Agile Project Plan
- Fundraising Plan
- Job Transition Plan
- Asset Maintenance Plan
- Maintenance Plan
- Software Test Plan
- Staff Training and Development Plan
- 3 Year Plan
- Brand Activation Plan
- Release Plan
- Resource Plan
- Risk Mitigation Plan
- Teacher Plan
- 30 60 90 Day Plan for New Manager
- Food Safety Plan
- Food Truck Plan
- Hiring Plan
- Quality Management Plan
- Wellness Plan
- Behavior Intervention Plan
- Bonus Plan
- Investment Plan
- Maternity Leave Plan
- Pandemic Response Plan
- Succession Planning
- Coaching Plan
- Configuration Management Plan
- Remote Work Plan
- Self Care Plan
- Teaching Plan
- 100-Day Plan
- HACCP Plan
- Student Plan
- Sustainability Plan
- 30 60 90 Day Plan for Interview
- Access Plan
- Site Specific Safety Plan
Garment Production Outline Plan
Prepared by: [Your Name]
Date: [Date]
I. Production Schedule
A. Overview
The production schedule outlines the entire timeline for the garment production process, ensuring each phase is completed efficiently, with room for quality control checks and adjustments. It begins with design finalization and extends through to the delivery of the finished garments.
B. Key Milestones
The timeline covers the production process over 12 weeks.
Week | Milestone |
---|---|
Week 1-2 | Design Finalization and 3D Digital Prototyping |
Week 3-4 | Smart Fabric Sourcing and Supplier Coordination |
Week 5 | Pattern Making Using Automated AI Tools |
Week 6-7 | Smart Textiles Production, AI-driven Sewing, and Cutting |
Week 8 | Initial Automated Quality Control with AI Visual Inspection |
Week 9 | Finishing, Adjustments, and Robotics-Assisted Final Touches |
Week 10 | Final AI-driven Quality Control and Packaging |
Week 11 | Sustainable Packaging and Inventory Tracking |
Week 12 | Delivery via Drone/Autonomous Vehicles |
II. Material Requirements
A. Fabrics and Trims
Materials required include advanced smart fabrics, threads, eco-friendly trims, and automated RFID chips for tracking. These materials are designed to be sustainable, with a focus on eco-friendly sourcing and the use of recycled components.
B. Supplier Coordination
Work closely with global suppliers using blockchain technology to ensure the traceability and authenticity of materials. AI-driven communication ensures real-time updates on material availability, reducing delays in the production schedule.
III. Task Breakdown
A. Design and Development
Tasks include sketching designs using 3D modeling software, selecting innovative smart textiles, and creating virtual patterns through AI-driven design tools. Designers collaborate with AI systems to predict consumer trends, ensuring styles are market-relevant and cost-efficient.
B. Sample Making
Smart sewing machines are used to create initial samples for review. 3D printing may also be used to produce intricate design elements such as custom trims or fastenings. Samples are sent to the virtual cloud for client review and instant feedback.
C. Cutting and Sewing
Bulk cutting is performed by automated laser-cutting machines programmed for precision. Sewing is AI-monitored to ensure accuracy and consistency, with adjustments made in real-time as the AI identifies potential issues.
D. Quality Checks and Adjustments
An initial round of AI-driven quality control ensures fabric quality, stitching accuracy, and seam integrity. Adjustments are made based on feedback from this automated system before the garments are sent for final inspection.
E. Finishing
Robotic machines press and fold garments, attach RFID labels for tracking, and package them in smart, biodegradable containers. Labels are embedded with AR technology, allowing customers to scan for product information.
IV. Resource Allocation
A. Human Resources
Allocation of tasks is highly streamlined. Designers focus on creative input while AI and robotics handle repetitive tasks. Quality control personnel oversee AI systems, while supervisors monitor overall workflow. Workers specializing in advanced textile technology are essential for managing smart fabrics and automated machines.
B. Equipment
Ensure availability of:
AI-driven sewing machines.
Automated cutting and pressing machines.
Digital fabric printers for design prototypes.
AR-enabled quality control scanners.
Smart textile assembly equipment.
V. Quality Control Procedures
A. Initial Inspection
Upon material arrival, automated AI systems scan for defects in fabric, trim, and accessories. Smart sensors measure fabric weight, thickness, and elasticity to ensure compliance with pre-set standards.
B. In-Process Quality Control
AI continuously monitors the production process. Real-time data on stitching, fabric integrity, and seam alignment is gathered, and potential issues are flagged immediately. Defective pieces are automatically set aside for adjustment.
C. Final Inspection
AI visual inspection and laser scanning are used to ensure garments meet all quality standards. This process includes evaluating aesthetic details, structural integrity, and smart fabric functionality. Only garments passing these checks proceed to packaging.
VI. Delivery Schedule
A. Packaging
Finished garments are placed into biodegradable, AR-enabled packaging. The packaging contains scannable data for the customer, including product care instructions, sustainability information, and product tracking via embedded RFID tags.
B. Shipment Coordination
Drones and autonomous electric vehicles are used for quick, efficient delivery. Logistics are coordinated through AI systems, ensuring optimized delivery routes to minimize carbon footprint.
C. Delivery Confirmation
Once the garments have reached the client, confirmation is sent automatically through blockchain-based verification systems. Client feedback is gathered using AI-driven survey tools, ensuring continuous improvement in the production process.
VII. References
Williams, A. & Green, T. (2050). Sustainable and Smart Garment Production: The Next Generation of Fashion Manufacturing. Future Textile Publishing.
Lee, S., & Patel, N. (2050). AI and Robotics in Garment Manufacturing: Revolutionizing the Apparel Industry. AI Insight.
American Apparel and Footwear Association. (2050). Smart Textiles and Blockchain in Apparel Manufacturing. Retrieved from https://www.aafaglobal2050.com